Electro Drum Magnets
Magnet | Electromagnetic Coils |
Material | Dry |
Conveying | Top-fed, Center-fed, Bottom-fed |
Separates | Large and Angular Ferrous Metals |
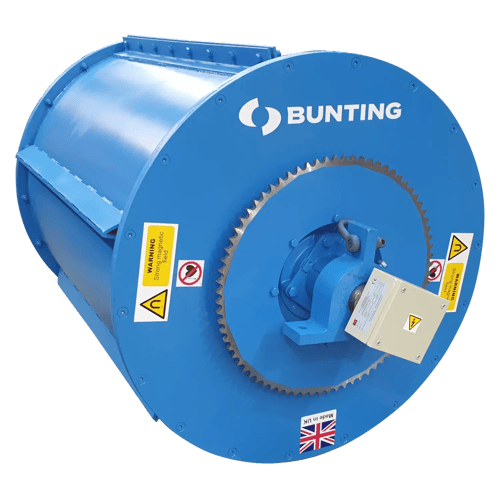
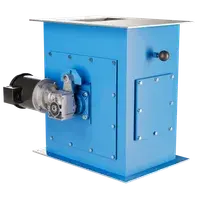
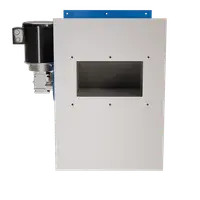
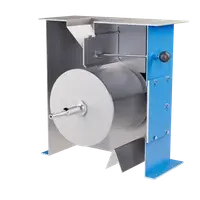
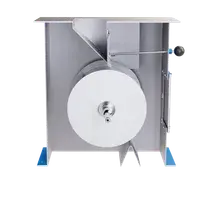
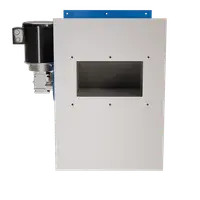
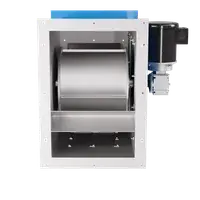
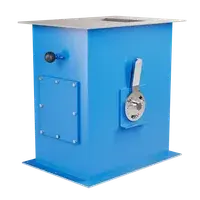
Animation
Key Features
Features a stationary electromagnetic coil within a rotating non-magnetic shell, ensuring efficient separation of ferrous materials.
Built to handle large, irregular ferrous items, making them suitable for challenging separation tasks.
Designed for uninterrupted processing, enhancing productivity in high-volume applications.
- About
- Benefits
- Operation
- Tech Specs
Electro Drum Magnets are advanced magnetic separators designed for heavy-duty applications, particularly in industries that require the efficient removal of ferrous metals from bulk materials. These powerful devices utilize stationary electromagnetic coils housed within a robust, non-magnetic shell, typically made of manganese steel. The shell rotates around the stationary coils, generating a strong magnetic field that effectively captures large and angular ferrous materials.
Our Electro Drum Magnets are engineered to handle the most challenging environments, making them ideal for applications in automotive recycling, municipal waste processing, and steelworks.
Available in two distinct models:
- Frag Electro Drum (FED): Designed for continuous removal of ferrous metals from product streams, maximizing purity.
- Slag Electro Drum (SED): Optimized for maximum metal separation efficiency by holding ferrous materials firmly against the drum throughout its rotation.
In addition to their robust construction and powerful magnetic capabilities, Electro Drum Magnets are customizable in terms of size and configuration to fit various operational requirements. This adaptability ensures that they can seamlessly integrate into existing processing systems, enhancing overall productivity and material purity.
Whether you are looking to improve metal recovery in recycling operations or ensure compliance with safety standards in food processing, our Electro Drum Magnets deliver exceptional performance and reliability. Explore how these innovative magnetic separators can optimize your operations.
Powerful Magnetic Field: Electro drum magnets generate a strong, adjustable magnetic field, allowing for effective separation of ferrous materials, even in challenging applications with large or angular metal pieces.
High-Volume Processing: Designed for heavy-duty applications, electro drum magnets can handle large volumes of material, making them ideal for industrial-scale operations in recycling and mining.
Customizable Design: Available in various sizes and configurations, these magnets can be tailored to specific operational needs, optimizing performance for unique processing requirements.
Durability: Constructed with robust materials like manganese steel shells, these magnets are built to withstand harsh industrial environments, ensuring long-term reliability and performance.
Manual magnetic arc adjustment: The ability to adjust the magnetic application point allows for fine-tuning of the separation process, maximizing the quality of recovered ferrous materials.
Electro Drum Magnets are engineered to excel in challenging, heavy-duty applications with large and angular ferrous metals. The substantial size and weight of these metal pieces require a powerful and deep magnetic field, which our Electro Drum Magnets generate using powerful electromagnetic coils.
Our Electro Drum Magnets offer three versatile feeding configurations to suit various process requirements:
- Top-Feed Configuration: Material is introduced at the top of the Electro Drum. Magnetic items are attracted and held to the drum's surface, then discharged beneath the drum.
- Bottom-Feed Configuration: Material is fed beneath the Electro Drum. Magnetic items are captured by the drum's surface, carried upward, and discharged over the top.
This flexibility in feeding arrangements allows our Electro Drum Magnets to integrate seamlessly into your existing processes, ensuring optimal separation efficiency for your specific application.
Magnet Type
Electromagnetic coils with stationary core
Shell Material
Non-magnetic manganese steel, typically 8-10mm thick. Replaceable wear covers as standard
Drum Diameter
Up to 1800mm (72")
Drum Width
Up to 3000mm (120")
Coil Design
FED Model: Single main coil with an auxiliary coil
SED Model: Multiple symmetrical coils (2-4 depending on width)
Coil Winding
Anodized aluminum foil or Nomex-covered aluminum wire.
Cooling System
Ducted coils for improved heat dissipation
Magnetic Arc
Adjustable for optimal separation
Application Photos
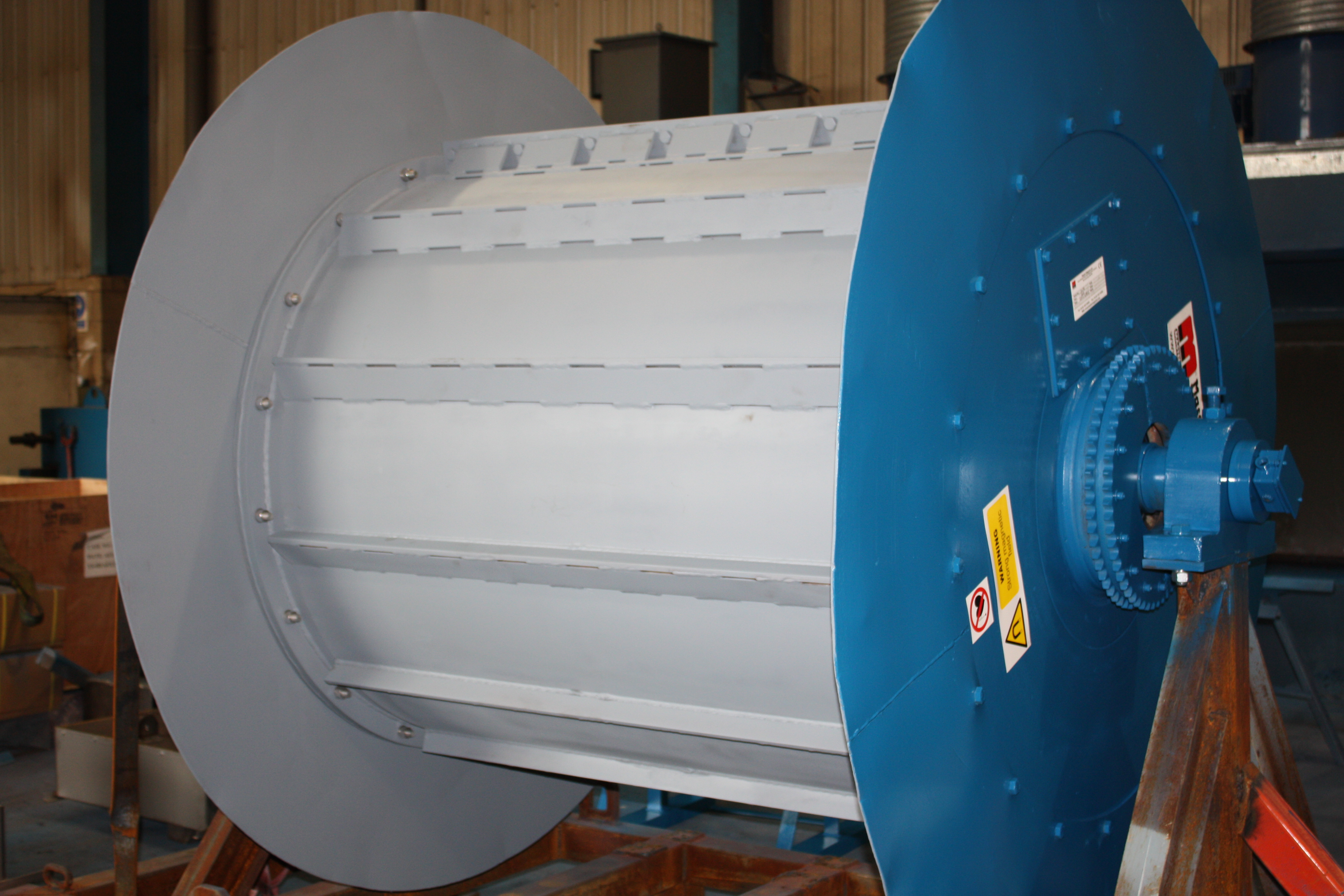
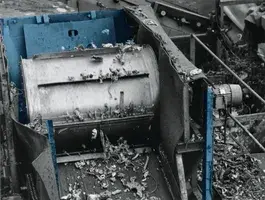
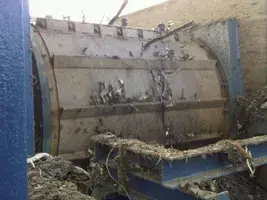
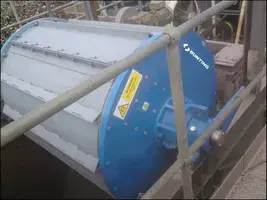


Want To Know More?
For more information, we encourage you to browse our website to view our extensive range of products, and to contact one of our sales representatives to discuss your specific needs and interests.