Get in touch with us at our toll-free number 1-800-835-2526 or request a quote here:
3 Metal Items Contaminating Plastic Waste – Magnetic Separation Solutions
Plastic waste recycling is an industry riddled with constant challenges. Even under the best circumstances, many factors unique to the manufacturing process present unique problems. One of these problems is the high prevalence of ferrous metal contamination found in plastic waste material being recycled. When ferrous metal contamination is present in plastic waste material, recycling becomes hindered by the serious damage metal contamination can cause to equipment. In addition to this downtime, metal contamination also hurts the process by compromising the quality of the end product. Fortunately, installing magnetic separation products from Bunting is a cost-efficient and highly effective way to reduce ferrous metal contamination and minimize these problems.
3 examples of ferrous metal contamination successfully removed by Bunting Magnetic Separation in a UK plastic waste recycling plant
Fine Metal Shards and Dust
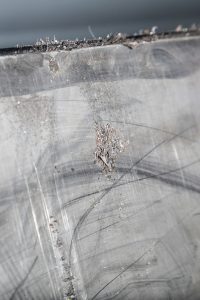
In this first example, the accompanying picture shows fine metal shards and dust captured on the surface of a plate magnet. This plate magnet, designed with powerful rare earth magnets, is capable of retrieving even the finest iron particles, lifting them up out of conveyed material and removing them from the material being processed. Fine iron contamination is notoriously difficult to separate from plastic waste, and ultimately results in significant wear to other equipment in the plant and a significantly compromised end product. While the contamination itself is often too difficult to see with the naked eye, the consequences of fine iron contamination can be seen from a mile away.
In this example, the plastics manufacturer installed plate magnetic separation both above conveyors and within chutes, where material is allowed to flow over the magnet’s face. In some installations, plastics waste recyclers choose to remove fine iron contamination automatically by installing a drum magnet, which provides continuous, maintenance-free operation. Both plate magnets and drum magnets are highly effective fine iron removal solutions.
Nuts, Bolts, and Screws
Larger ferrous contaminants, such as nuts, bolts, and screws, are typical examples of easy-to-spot metal contamination in plastics recycling. These objects can be present in the reclaimed plastic that is delivered to a facility, or they can be introduced into a process because of natural machine wear in the plant or routine maintenance. Regardless of how this metal contamination enters a process, the results are the same.
Larger metal contaminants like nuts, bolts, and screws can cause significant damage to other equipment in a processing plant, and frequently lead to highly expensive equipment repairs in addition to costly production downtime. In this example, a Bunting pulley magnet was used to effectively remove this type of metal contamination. Engineers replaced a standard head pulley on a conveyor with a pulley magnet, creating a simple, integrated magnetic separation solution. With the pulley magnet installed, its magnetic field now attracts and holds ferrous metal contamination from material being conveyed. The pulley magnet then deposits contamination beneath the conveyor and out of the way of the greater product stream.
Large Wrench
One of the most extreme items retrieved by Bunting magnetic separation was a large wrench! While seeing an entire wrench removed from a plastics processing line is shocking, it’s not unusual. When a tool like this enters a plastics stream, it can cause enormous amounts of damage, and quickly results in a sky-high bill for equipment repair costs and production downtime. It’s not difficult to imagine how much damage an item like this can cause—just imagine if it were to enter a shredder or granulator!
Fortunately, this wrench was able to be removed thanks to a Bunting pulley magnet. Depending on how a plastics processing plant is laid out, large ferrous metal contamination like this wrench may also be removed using a drum magnet or a crossbelt magnet.
Total Magnetic Separation Solutions from Bunting
In addition to the products that have already been mentioned, other Bunting products such as Eddy Current Separators (to remove non-ferrous metals such as aluminum) and metal detectors (to remove non-ferrous metals and stainless steel) are also commonly used in plastic waste recycling operations. Bunting’s expert engineers work one-on-one with plastics processing plants in order to assess optimum locations for magnetic separators and metal detectors to be installed, as well as recommending the best type of equipment for each process at each critical point.
Bunting provides total magnetic solutions for plastics recycling processors and more. To learn more about removing metal from plastic waste and our ability to create a metal removal solution for your plant, Contact us Today.