Get in touch with us at our toll-free number 1-800-835-2526 or request a quote here:
5 Key Eddy Current Separator Operating Parameters
Around the world, recycling plants rely on Eddy Current Separators to separate and recover various types of conductive non-ferrous metals. An Eddy Current Separator works by utilizing high strength magnetic forces that repel and eject non-ferrous metals. Examples of materials separated by an Eddy Current Separator include aluminum soda cans, aluminum foils in discarded packaging, and different sizes of scrap metal and wire from ASR and ICW automotive, appliance, and electronic recycling applications.
The first Eddy Current Separator was developed by the Bird Group, a UK-based metal recycler, in 1981. The development of the Eddy Current Separator was so significant that it resulted in the Bird Group being presented with the Prince of Wales’ Award for Technology and Innovation and the Tomorrow’s World Award to Technological Development and Innovation. The design of the Eddy Current Separator permanently changed the landscape of metal recycling by making it much easier and more efficient to separate and recover highly valuable non-ferrous metals like copper and aluminum. In the years that followed its initial invention, Eddy Current Separator technology has continued to grow and evolve.
There are many different suppliers who each offer their own unique designs of Eddy Current Separators, all with varying separation abilities.
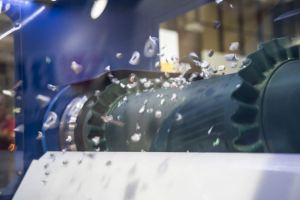
In order to successfully separate non-ferrous metals with an Eddy Current Separator, there are several key criteria to consider. This technical review assesses five of the key design characteristics of the Eddy Current Separator, and aims to dispel some common myths about this piece of equipment. The five design characteristics we will go over are:
- The rotational speed of the magnetic rotor
- The speed of the feed belt
- The length of the feed belt
- The necessity of pre-removing ferrous metal
- The relative magnetic strength of the rotor
1. Rotor Speed
An Eddy Current Separator’s design is based around a magnetic rotor that has alternating magnetic poles (north/south) which are continuously rotating within a non-metallic shell that is also rotating, but at a slower pace. A urethane feed belt rotates at the same speed as the non-metallic outer shell, and this feed belt conveys material into the higher rotating speed magnetic field that the rotor generates. Here, non-ferrous metals become induced by magnetically-driven eddy currents. In the non-ferrous metal particle, the eddy currents generate an electric current. Then, the non-ferrous metal particle will produce its own magnetic field. This new magnetic field will then react with the rotor’s magnetic field, creating a repulsive effect that causes the conductive non-ferrous metal to be repelled and, therefore, separated from the original product stream.
This separation is in accordance with two laws:
Faraday’s Law of Induction: This law relates to where electrical currents are induced when conductors enter a rotating magnetic field. For example, a conductor may be a non-ferrous metal such as a piece of aluminum or copper.
Lenz’s Law: In this law, the induced eddy currents create a magnetic field that opposes the magnetic field that initially created it. As a result, the conductor metal will be repelled away from the magnetic source.
Theoretically, if there was an increase in the number of polarity charges per second, there would be a positive effect on separation efficiency (i.e., more flux change would generate a greater reactive magnetic field in the non-ferrous metal). However, tests investigating this theory have shown that as rotor speed increases (and the rate of change of polarity changes increases), the actual displacement or thrown distance of a non-ferrous metal particle reaches a peak. Once it has reached this peak, the displacement of the non-ferrous metal particles will either be sustained or will even fall. This fall can be significant in the case of smaller particles.
When the relationship between magnetic rotor speed and the throw distance of a non-ferrous metal particle was investigated further, it was found that the amount of repulsive energy induced into a non-ferrous metal particle is proportional to the dwell time in the field. A shorter dwell time results in less induced energy. Therefore, the reduced energy leads to a reduction in the displacement or throw of a non-ferrous metal particle.
Other considerations to make in terms of rotor speed include maintenance and wear. When the rotor speed is increased, key components such as bearings experience a higher wear factor.
In practice, every magnetic rotor design has an optimum rotational speed that will produce the best level of non-ferrous metal displacement for each application. Commonly, this speed is between 2,000 and 5,000 RPM. There is a perception that an increased rotor speed or frequency will always result in a higher level of non-ferrous metal separation, but this perception is misguided.
• Eddy Current Separator Technical Overview by Prof Neil Rowson
2. Belt Speed
An Eddy Current Separator’s belt is the mechanism that conveys material into the head pulley magnetic rotor’s rotating magnetic field. The belt’s speed is the factor that will determine the conveyor’s burden depth, the material’s dwell time in the magnetic field, and what the trajectory of the material will be when leaving the belt.
Burden Depth
To achieve optimum separation, there must be a monolayer of material that is uniformly thin. A two-stage feed system produces the ideal feed characteristics. As the initial step in the process, a vibratory feeder will evenly spread feed material across the entire width of the tray. The width of this tray will be slightly narrower than the Eddy Current Separator’s belt width. Then, this material will be fed onto the Eddy Current Separator’s faster moving belt, which then spreads the material out further so that it attains a single particle depth. This lowering of the burden depth to a monolayer increases separation efficiency by reducing the risk that non-ferrous metal particles will collide with non-metallic materials.
Dwell Time
The dwell time of a particle in the rotating magnetic field is dictated by the speed of the belt the particle is traveling on. If there is a longer dwell time, more energy will be induced into the conductive non-ferrous metal particle. In an extreme example, if aluminum is allowed to remain in the rotating field for too long, it will become exceptionally hot and anneal. At the other end of the spectrum, a belt speed that is too high will transfer material through the magnetic field too quickly, thus reducing the separation effect.
Material Trajectory
The belt speed of any conveyor will create a trajectory of material as it leaves the belt. When in operation, higher belt speeds result in longer and higher projections of conveyed material being sent away from the head pulley. In order to achieve successful separation of non-ferrous metals on an Eddy Current Separator, it is essential to understand all forces that are impacted on the particles, including belt speed.
The forces a non-ferrous metal particle is subject to upon entering the Eddy Current Separator’s rotating magnetic field include:
• Eddy Current repulsion force from the magnetic rotor
• Conveyor propulsion that is proportional to the belt speed
• Gravity
Combined, these three forces produce a resultant force that then will determine the non-ferrous metal particle’s trajectory.
The Eddy Current repulsion—here, force A—will only generate a reaction in a conductive non-ferrous metal particle. Meanwhile, forces B and C affect all of the material on the conveyor belt. This means that if the size, shape and weight of every particle on the conveyor was the same, and there was no magnetic rotor to factor in, the throw trajectory would be the same. When Eddy Current repulsion is factored in, the trajectory of the non-ferrous particle is altered, propelling it upward and away from the magnetic rotor.
When an Eddy Current Separator is being commissioned, technicians will often initially run non-metallic material over the unit so that they can check the material trajectory in order to correctly position the splitter. Adding non-ferrous metal fraction allows the two trajectories to be compared, and then the optimum setting of the splitter can be determined. This splitter enables non-metallic and non-ferrous metal constituents to be separated from each other.
However, in the case that Force B—the forward force from the feed belt—is increased, while all other forces remain constant, the resultant force vector will flatten and reach a point where the trajectories of non-metallic materials and non-ferrous metal particles either cross each other or become almost identical. In this situation, the limited difference between the two trajectories will prevent optimum separation from being achieved.
Because different Eddy Current Separators will have different designs of magnetic rotors, and because the shape, size, and other characteristics of non-ferrous metal particles can vary so widely, there is no such thing as a one-size-fits-all belt speed. To determine the optimum belt speed, the application and installation must first be taken into account.
3. Feed Belt Length
The conveyor belt length of an Eddy Current Separator can vary significantly. Part of this is due to claims that longer belts will improve the level of separation achieved. To determine the belt length, engineers analyze the function of the belt and how it will interact with the other parts of the greater separation system.
The job of a conveyor belt is simple—to transport the material into the rotating magnetic field, also referred to as the “separation zone.” In order to achieve optimum separation, material will be settled and ideally still on the conveyor belt prior to entering the separation zone. Longer conveyor belts allow a longer dwell time for material to settle.
However, material particles settle quicker when they are fed onto the belt via a vibratory feeder. The vibratory feeder action evenly spreads material across the tray’s width before it is gently dropped onto the more rapidly moving belt. This causes the material to be splayed even more. But, minimizing the drop height from the vibratory feeder to the belt minimizes product bounce and settles the stream faster, which must be settled before the stream hits the magnetic field. In practice, utilizing a vibratory feeder eliminates the need for Eddy Current Separators to have long conveyor belts.
In some specialized applications, material being fed directly from a vibratory feeder (with a non-metallic trap or tray tip) into the separation zone can remove the need for any belt at all. However, the belt is still important, as it functions as a cleaning device that transports any attracted magnetic material out of the product stream and away from the Eddy Current Separator’s rotor shell.
4. Ferrous Metal Removal
Even though the Eddy Current Separator is a system based on magnetic principles, there is often confusion regarding the separation of ferrous metals.
In short, the Eddy Current Separator has two pulleys and a belt. One of these pulleys is magnetic. Because of the laws of physics, the magnetic head pulley (or rotor) attracts ferrous metal. Therefore, the system would separate non-magnetic metals from ferrous magnetic metals. However, there are some limitations associated with this.
Concentric Rotors
An Eddy Current Separator using a concentric magnetic rotor design has a magnetic rotor that maintains the same gap between the outer non-magnetic shell and the internal magnets throughout the entire circumference of the rotor. The high-strength magnetic rotor is constructed with powerful neodymium rare earth magnets that hold ferrous metal tightly in place—at the expense of making it difficult to discharge from the belt. Additionally, because of the high-speed rotating magnetic field, ferrous metal that cannot be discharged instead remains on top of the belt at the bottom point of the magnetic rotor. Because the magnetic field is constantly rotating and changing, the metal vibrates and becomes very hot. As a result, once the conveyor belt stops, this red hot ferrous metal can easily burn a hole through the belt and onto the non-metallic shell’s surface. Over time, continuous wear resulting from ferrous metal will lead to deterioration and holes on the non-metallic shell’s surface. Then, attracted ferrous metals will pass through these holes and attach to the rotor magnets, leading to catastrophic failure of equipment. So, in these scenarios it is important to have maximum magnetic separation of the material upstream before the stream lands on the Eddy Current belt.
Eccentric Rotors
An Eddy Current Rotor utilizing an eccentric magnetic rotor design mounts a smaller rotor in the top quadrant of the non-metallic shell. In this design, attracted magnetic material will move through a diminishing magnetic field until it ultimately reaches a point where it falls away from the belt. This ferrous metal then often discharges into the non-metallic fraction. But, even in this scenario, upstream magnetic separation is critical to minimize the amount of ferrous material coming in contact with the Eddy Current field.
Best Practice
In order to achieve optimum metal recovery and separation, a multi-staged approach must be implemented, with specific materials being recovered at different stages. Installing upstream magnetic separation such as a magnetic crossbelt, pulley magnets, and drum magnets allows for successful recovery of valuable ferrous metals prior to material being introduced to the Eddy Current Separator. Most systems will utilize dual magnetic separation with a magnetic crossbelt, and then either a neo magnetic head pulley or a neo magnetic drum separator before the stream hits the Eddy Current belt. This then allows for safe non-obstructive separation and recovery of the non-ferrous metals on the Eddy Current Separator.
5. Rotor Magnetic Strength
Earlier, we saw the laws of Faraday and Lenz suggest that the strongest rotating magnetic field would be able to produce a greater repulsive effect. In operation, however, this has been proven not to be the case.
An Eddy Current Separator’s rotor is constructed from several strong permanent magnets. These magnets may be either neodymium rare earth or ceramic ferrite, and are attached to a steel carrier. The permanent magnet’s dimensions—both its arc length around the rotor as well as its block thickness—will dictate the throw of the magnetic field.
• A magnet that is longer and thicker will produce a deeper magnetic field.
• A magnet that is shorter and thinner will produce a shallow, intense magnetic field.
Regardless of if a magnet is long or short, the maximum magnetic intensity will occur on the pole (or surface) of the magnet that is mounted on the magnetic rotor’s carrier. A key parameter in design focuses on minimizing the distance between the surface of the belt and the magnetic pole, as the strength of a magnetic field decreases as distance increases. This distance is influenced by four variables:
1. Carbon fiber wrap: Magnets are positioned to sit on the rotor’s magnet carrier, which independently rotates within the non-magnetic shell. To securely hold the magnets to the carrier, carbon fiber tape is wrapped around the magnetic rotor assembly.
2. Air gap: There must be a sufficient air gap between the surface of the carbon fiber tape and the inside of the shell to ensure no contact occurs, even when there may be a small degree of flexing when the rotor is spinning at high speeds.
3. Shell thickness: In order to withstand wear and tear caused by punishing work environments, the shell must be sufficiently thick to resist deflection across wider conveyors.
4. Belt thickness: Belts also must be designed to withstand difficult working conditions, and some applications will require thicker, more robust feed belt designs and others can utilize thinner urethane belts to minimize the gap.
When carbon fiber wrap, internal air gap, shell thickness, and belt thickness are all accounted for, there will be several millimeters of space between the belt’s surface and the point of maximum magnetic strength. After these parameters have been set, the next step is to determine what the expected performance of rotors with short or long magnets will be.
Shorter magnets produce an intense magnetic field, but the field is shallower in height. The magnetic intensity drops off quickly as you get to the surface of the belt—and the magnetic field on the belt surface is lower than on the face of a magnet. Comparatively, longer magnets are able to throw a deeper magnetic field. When applying this information in practice, it means that a magnetic rotor with short, yet exceptionally strong neodymium rare earth magnets may ultimately produce a weaker magnetic field on the belt surface compared to a rotor constructed from longer standard strength ferrite magnets at the point of separation (i.e., on the surface of the belt).
A shallow or deep magnetic field has a big effect—it means that classifying a magnetic rotor as “strong” or “weak” will ultimately be completely dependent on where the measurement supporting that description is taken. For example:
ROTOR DESIGN | ON THE SURFACE OF THE BELT | 10MM ABOVE THE SURFACE OF THE BELT |
Rotor 1 – Short, exceptionally strong Rare Earth Neodymium Magnets with a shallower field
|
Strongest | Weaker |
Rotor 2 – Long, standard strength Ferrite Magnets with a deep field
|
Weakest | Strong |
Rotor 3 – Long, exceptionally strong Rare Earth Neodymium Magnets with a deep field
|
Strong | Strongest |
Table 1: Eddy Current Separator rotor comparisons
Ultimately, the application an Eddy Current Separator is being used in will always dictate the selection of magnetic rotor design. For example, if the aim is to project a magnetic field into the center of a large non-ferrous particle, such as an aluminum can, a rotor with longer magnets that can produce a deep magnetic field will be best. As another example, if the goal is the separation of small non-ferrous metal particles, such as those found in ground plastics, it is better to use a rotor with shorter magnets and a shallower, more intense magnetic field.
It is vitally important to understand these principles when considering what design and type of Eddy Current Separator will best suit a specific application. It is not enough to be told that the magnetic field is the “strongest on the market,” as this will not determine if that Eddy Current Separator rotor design is truly able to offer the optimum level of separation.
Selecting an Eddy Current Separator
To select the optimum non-ferrous metal separator, understanding the application it will be used in is key. Our engineers consider the following:
Material:
• What the material is, and what form it is in
• How material is being fed
• Has ferrous material been removed from the stream?
• Particle size range (typically between 3mm and 50mm)
• Non-ferrous metal particles
• Shape of non-ferrous metal particles (e.g. angular, wire, spherical, etc.)
• Moisture level of the feed
• Separation objective
• % recovery objective
• % purity objective
Installation:
• Feed conveyor width, or how the material will be fed
• The type of magnetic ferrous separation to utilize, or if magnetic ferrous separation is already installed upstream
• Flow capacity desired by the customer
• Type of feeding to utilize to get the speed and burden depth desired