NEWTON, Kan. (June 19, 2025) — Robert (Bob) Bunting, chairman of Bunting Magnetics and a key figure in the company’s growth into a global supplier and manufacturer of magnetic solutions, died Tuesday, June 17, surrounded by family. He was 76.
Bunting, headquartered in Newton, Kan., is a family-owned company founded in 1959 by Walter Bunting. Bob Bunting, Walter’s son, led the company for nearly three decades, overseeing its expansion into international markets and the diversification of its product lines during his tenure as president and CEO.
“My father dedicated his life to this company,” said Robert Bunting Jr., Bob’s son and current president and CEO of Bunting. “He was a tireless worker whose vision and determination shaped Bunting into the company it is today. He held high standards and pushed us to be our best, but those who knew him understood it came from a place of deep care—for the people who worked here and the future he was building for all of us.”
Under Bob Bunting’s leadership, the company expanded its global footprint, establishing operations in the United Kingdom, China and Australia, along with additional facilities across North America. He preserved Bunting’s identity as a family-owned business while championing innovations that positioned the company as a trusted partner to manufacturers and producers across a broad range of industries worldwide.
In addition to his corporate leadership, Bob Bunting was deeply committed to giving back to the community. He and his family consistently supported charitable, educational and civic initiatives across Newton and the surrounding region. Their longstanding support included the United Way, the Newton Public Library Foundation, and the regional YMCA project. In recognition of their leadership and generosity, Bob and his wife, Barbara, were honored as Philanthropists of the Year by the Newton Public Library Foundation and acknowledged by the Central Kansas Community Foundation.
Bob also believed strongly in supporting Bunting employees and their families. Under his guidance, the company established the Walter F. and June A. Bunting Memorial Scholarship Fund to help the children of employees pursue higher education. Whether through public gifts or quiet contributions, Bob’s commitment to community reflected his deep belief that strong companies are built by strong, supported people.
Bob Bunting’s legacy continues through the company he helped shape, the community he championed, and the people whose lives he touched along the way. His vision, generosity and belief in hard work will continue to guide Bunting for generations to come. As we move forward, we do so with deep gratitude—for his leadership, his example, and the enduring values he instilled in all of us.
About Bunting Magnetics
Bunting is a global leader in magnetic separation, metal detection, and conveyor equipment for a wide range of industries, including food processing, plastics, recycling, mining, and pharmaceuticals. Founded in 1959, Bunting remains a family-owned company committed to helping customers protect their equipment, their products, and their brands.
The company also operates Magnet Applications, which sources, engineers and manufactures custom magnets and magnetic assemblies for critical applications including automobiles, electric motors, sensors and medical equipment. In addition, Bunting produces high-precision printing cylinders for decorating two-piece cans, serving customers in the packaging and beverage industries.
NEWTON, Kan. — Bunting Magnetics has officially unveiled their new state-of-the-art manufacturing facility in Newton, Kansas, expanding its global production of magnetic cylinders used in aluminum beverage can printing. The facility was introduced to the public for the first time during a ribbon-cutting ceremony. The event marks a major milestone for the company, which supplies critical components to companies that produce aluminum cans and aerosol cans.
The 16,000-square-foot facility features robotic machining systems and climate-controlled operations that maintain tolerances within 1/10,000 of an inch. Many of the aluminum beverage cans printed worldwide rely on Bunting cylinders, which are essential tools for fast, precise label changes in high-speed can production.
“This facility allows us to scale production while maintaining the extreme precision our customers depend on,” said Robert Bunting Jr., president and CEO. “It’s a significant step forward in our mission to be a world-class provider of magnetic solutions.”
The cylinders use magnets to snap metal printing plates into place, enabling fast plate changes and intricate designs. The new automated fabrication line operates 24/7, including unattended overnight shifts. To ensure precision, temperatures inside the facility are kept within a four-degree range (68–72°F). During assembly, parts are cryogenically cooled to -80°F to create a permanent, interference fit as they return to room temperature.
Bunting is also relocating equipment from their recent TD Wright acquisition in Minnesota to the Newton site, expanding capabilities and creating new local jobs. The company currently employs about 100 people in Newton and 240 globally.
“We’re proud of our legacy here, and this facility represents the next chapter,” said Bob Bunting, Chairman of the Board. “It’s about investing in the future and creating opportunity.”
Founded in 1959, Bunting remains a global leader in magnetic separation, metal detection, and industrial conveyors for industries including food processing, plastics, recycling, and more.
Despite global pressures, Bunting remains committed to innovation, investment, and strengthening American manufacturing.
For more information, visit www.buntingmagnetics.com
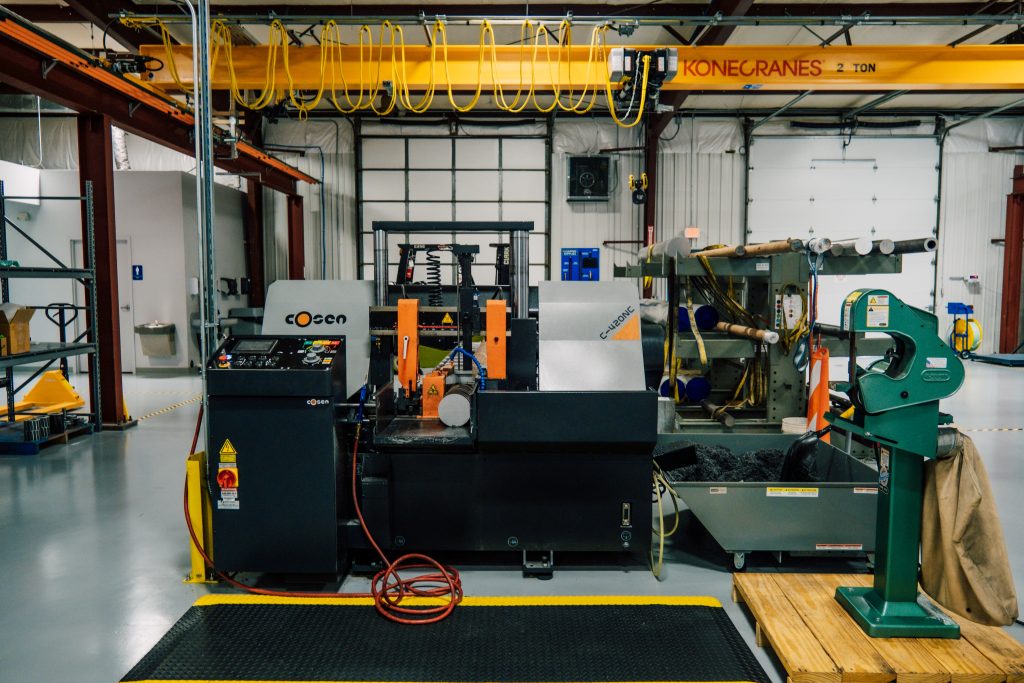
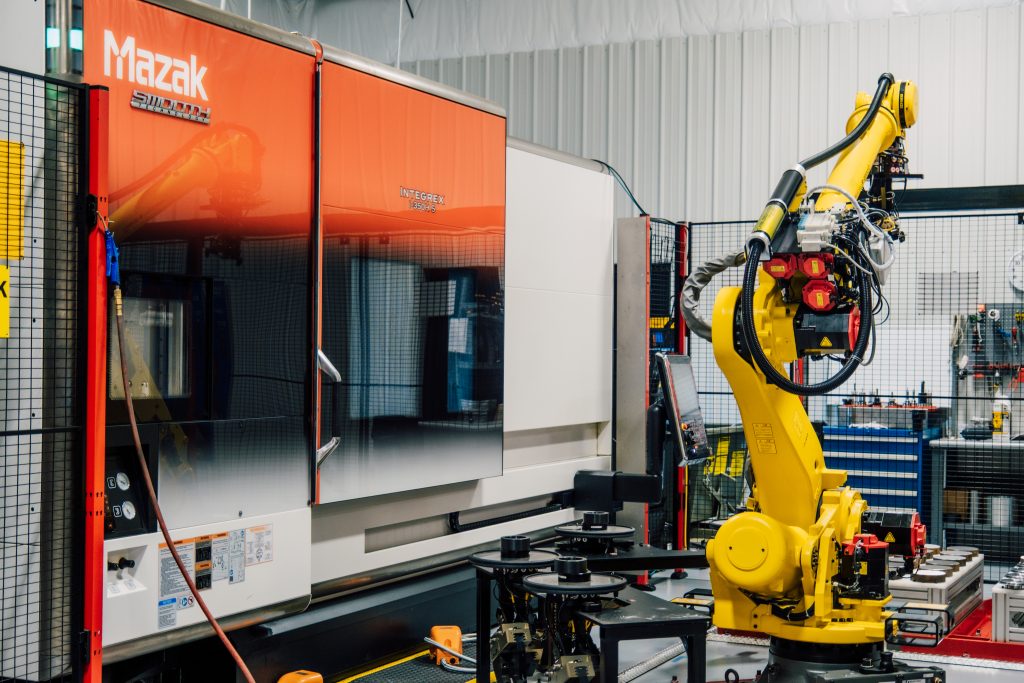

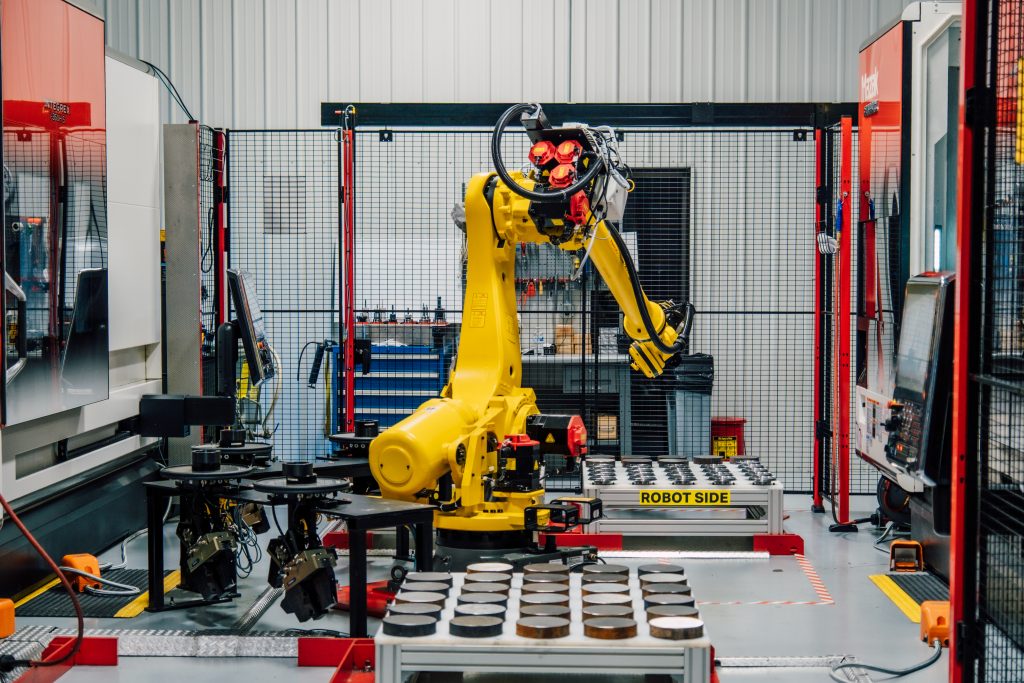
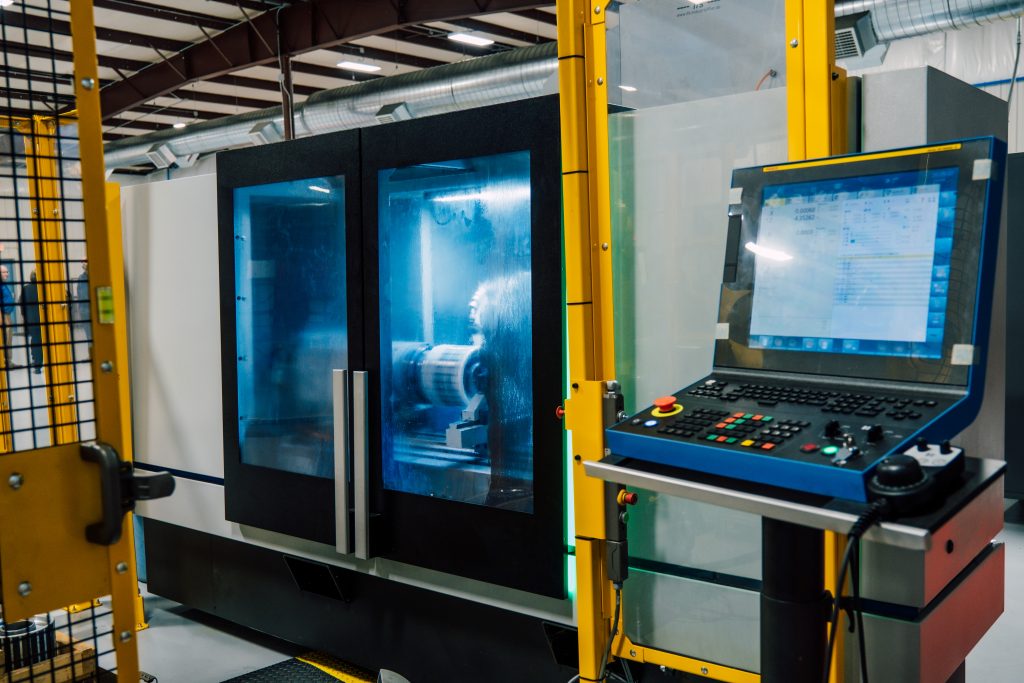
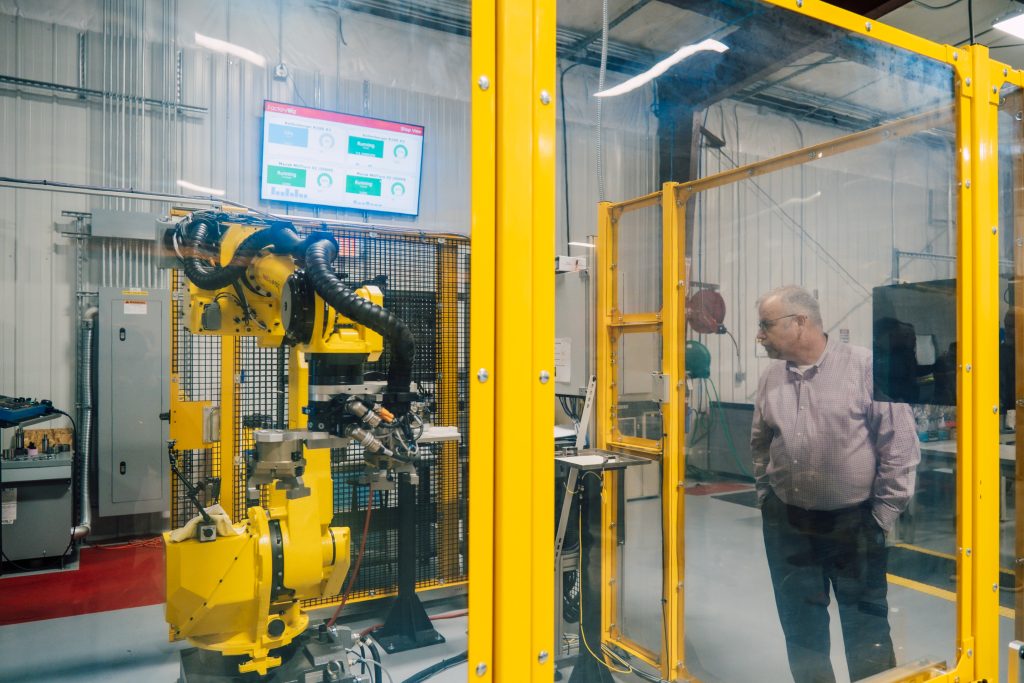
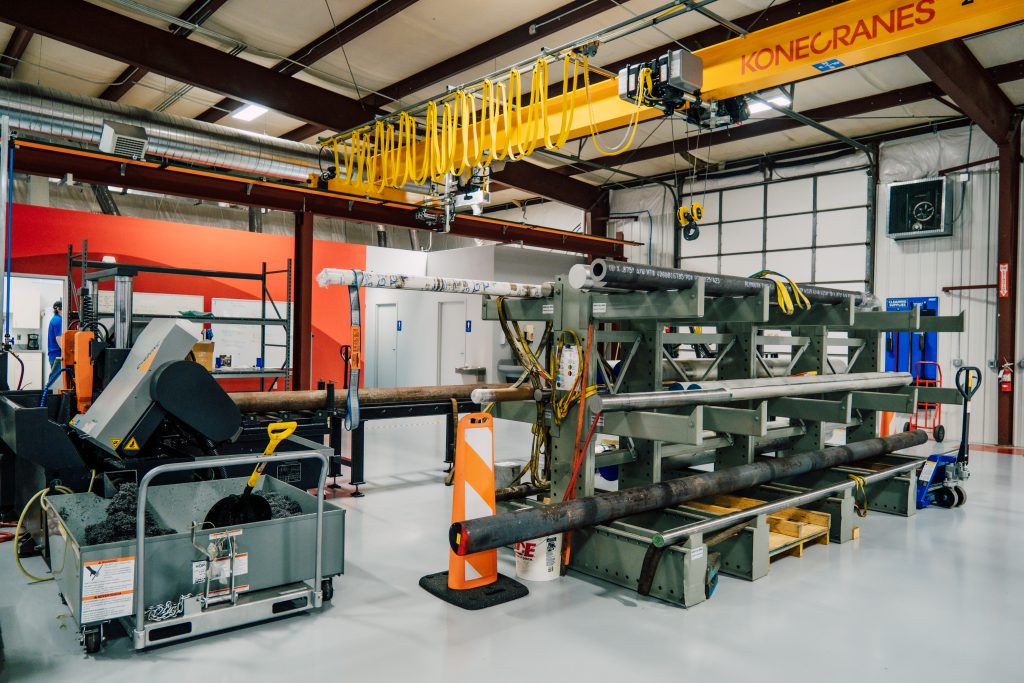
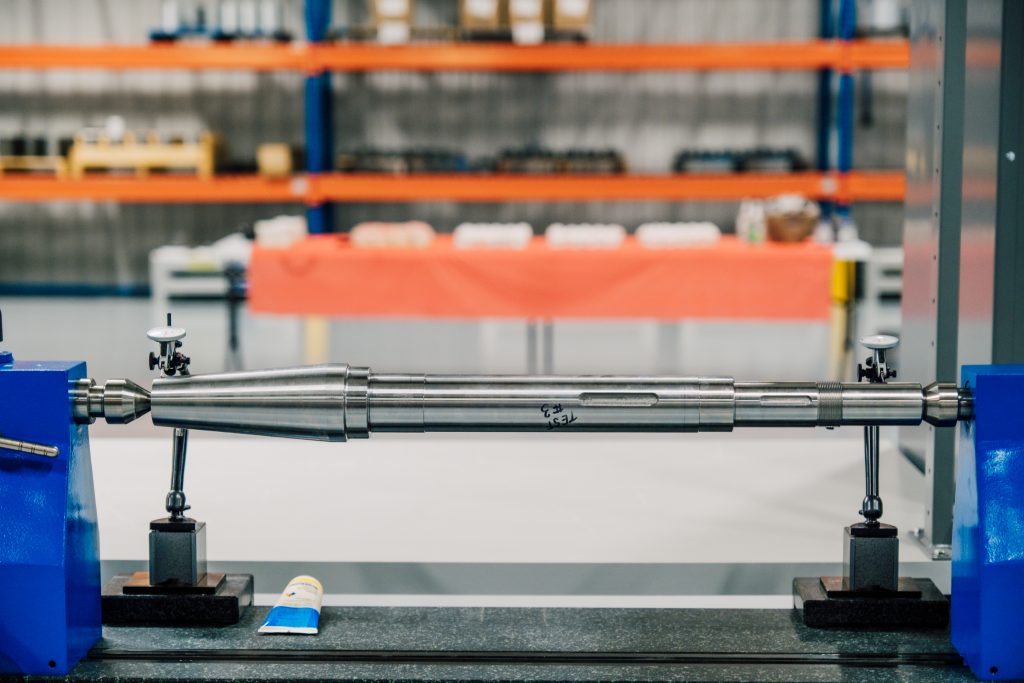
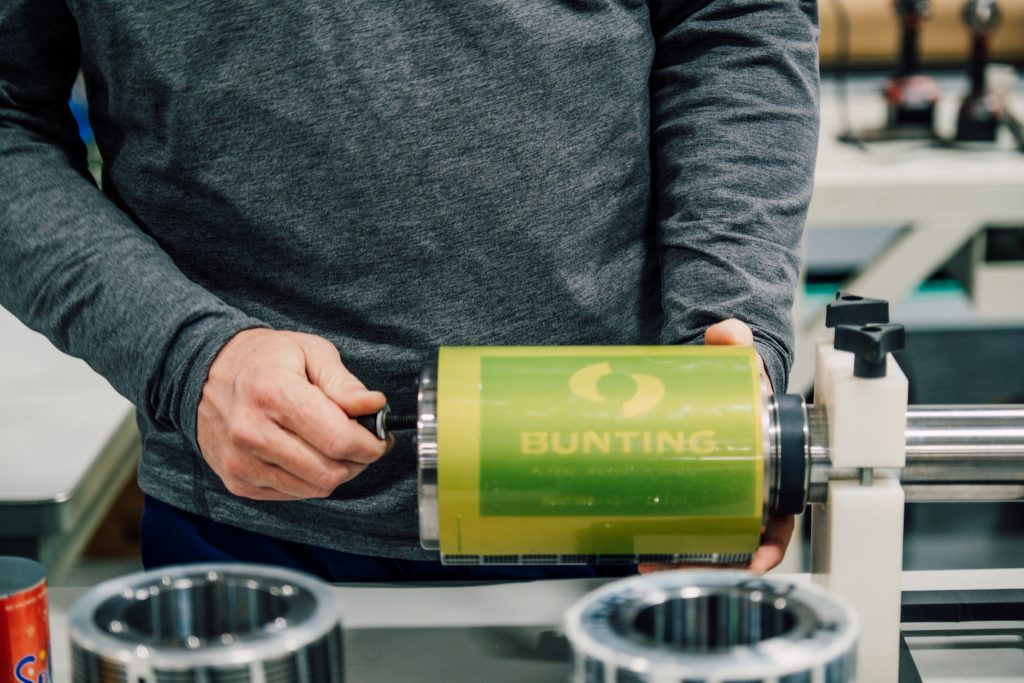
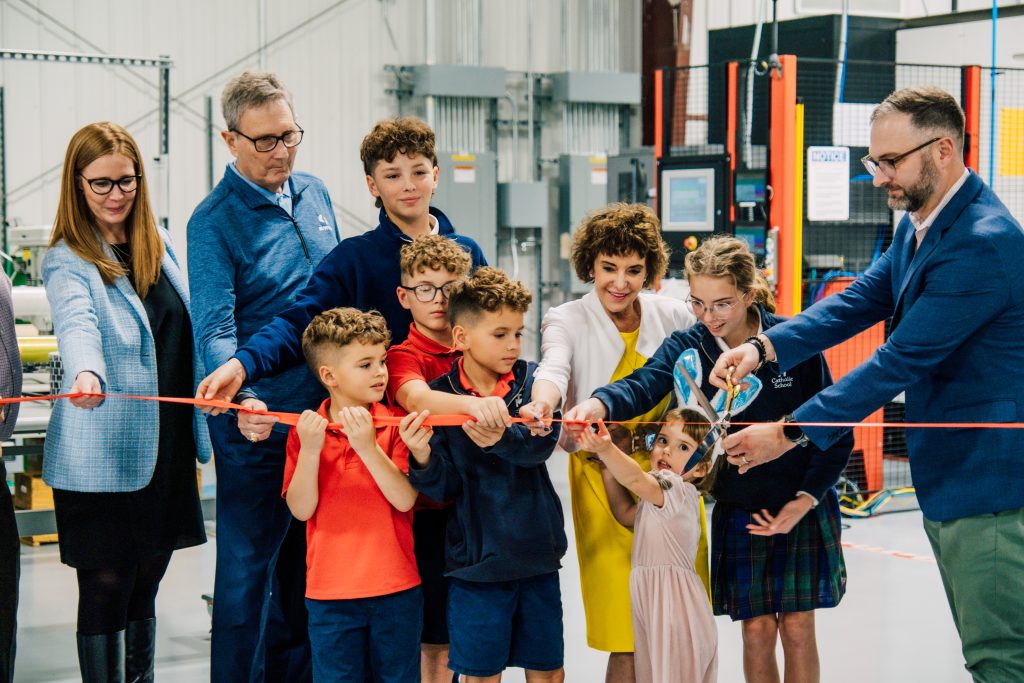
Mining and quarrying operations inevitably contend with tramp metal. The very act of extracting ore and aggregate using large, heavy equipment introduces a variety of metallic contaminants into the raw material. Operators must identify and remove this metal to prevent costly damage to processing equipment like crushers, screens, and conveyors. Moreover, many end-customers, especially power stations that use coal, specify maximum metal contamination levels in the delivered ore. This article explores the optimum magnetic separation methods that mining and quarrying operations employ to solve tramp metal removal problems.
The Origin of Quarrying and Mining Tramp Metal
For effective tramp metal removal, operators must first pinpoint its origins and characteristics. We define ‘tramp metal’ as any foreign metallic object that does not naturally occur within the extracted ore or aggregate. This includes contaminants like digger teeth, pit props, blasting caps, nuts, bolts, and metal fragments that result from process plant wear. Mining operations typically execute a multi-stage recovery of valuable ore. They reduce the ore’s particle size through crushing and milling, which liberates the ore from the gangue—the unwanted material. Then, they segregate the ore into specific size fractions using screening. Quarrying operations follow a comparable process for aggregates. In both mining and quarrying, these processing stages place equipment at high risk of damage from tramp metal.
Protecting Processing Equipment: Tramp Metal Risks
Mining and quarrying operations expose critical processing equipment to the constant threat of tramp metal. Operators must safeguard these machines to maintain efficiency and prevent costly downtime.
Crushers
Operators utilize various crushing technologies to reduce ore and aggregate size across multiple stages. They primarily employ jaw and gyratory crushers for initial crushing, which leaves these machines vulnerable to large tramp metal impacts. Cone crushers, favored for secondary, tertiary, and quaternary stages, demonstrate high sensitivity to even small metal contaminants. Impact crushers, versatile machines, function at any crushing stage.
Jaw Crushers
Jaw crushers compress rock between a stationary and a mobile jaw. A pitman powers the moving jaw’s reciprocating motion. This crushing action breaks large boulders into smaller pieces. Tramp metal that enters the jaws damages the surface liners, compromising crushing efficiency and size accuracy. Large rogue metal pieces necessitate liner and pitman replacements.
Gyratory Crushers
Gyratory crushers feature an oscillating shaft that reduces material within a crushing cavity. An external bowl liner and an internal mantle, mounted on the oscillating shaft, perform the crushing. Continuous compression between these liners fragments the material. Additional crushing occurs as compressed particles interact, minimizing liner wear. Tramp metal severely damages the central mantle and can block the output. Blockages strain the system, leading to catastrophic internal crushing mechanism failures.
Cone Crushers
Cone crushers, similar to gyratory crushers, process smaller particle sizes. An eccentric shaft, driven by a gear and pinion, powers the main shaft’s oscillation. This oscillation causes the cone head to move between open and closed discharge settings. Crushing happens through continuous compression between the liners. Like gyratory crushers, cone crushers experience damage to the central mantle, concave, and bowl liner from tramp metal. Their operating nature makes them especially sensitive to all sizes of metal. High repair costs and component replacements result.
Impact Crushers
Impact crushers come in horizontal shaft impact (HSI) and vertical shaft impact (VSI) types. HSI crushers reduce feed material size through high-intensity impacts from rotor-mounted hammers or bars. Further fragmentation occurs as particles collide within the crusher chamber. VSI crushers, used in final crushing stages, produce precise cubical shapes. They function like centrifugal pumps, accelerating material through a rotor. The material crushes against the outer body and through particle collisions. Tramp metal damages rotors and impact plates, incurring significant repair costs and lost production revenue.
Safeguarding Screens: Maintaining Size Integrity in Mining and Quarrying
Mining and quarrying operations deploy diverse screen designs to meet varied processing needs, including dewatering, grizzly, linear, and trommel screens. Operators must protect these screens to ensure efficient material separation.
Grizzly and Trommel Screens
Operators typically position grizzly and trommel screens between the primary feeder and crusher. Grizzly screens direct mined rock across inclined, parallel steel bars or rails. They construct these screens from heavy-duty manganese steel or high-impact alloys for superior wear resistance. However, large, elongated tramp metal pieces can inflict damage. Similarly, elongated tramp metal causes wear, damage, and blockages in trommel screens, where mined rock enters large-diameter rotating drums. Trommel hole sizes determine screening particle size, with single trommels often separating multiple size fractions. Tramp iron obstructs trommels and damages the holes, altering sizing accuracy.
Linear Screens
Operators use single and double-deck linear screens for finer particle segregation later in the process. These screens employ various media, including wire and urethane, both vulnerable to tramp metal damage. Tramp metal can break metal wire screens, contaminating post-screened rock with new, smaller metal fragments. Tramp metal punctures or cuts urethane screens, affecting screening efficiency. Undetected screen damage leads to failures in meeting strict product sizing requirements.
Dewatering Screens
Dewatering screens remove moisture from materials, particularly in aggregate and mineral processing. Tramp metal impacting the inclined, linear-motion screen damages the screen surface, significantly reducing sizing efficiency.
Tramp Metal Removal: Strategies for Protection
Mining and quarrying operations tailor tramp metal control strategies to the specific rock, process, and contaminants present. They primarily employ magnetic separation and metal detection equipment to prevent processing plant damage.
Magnetic Separation
Magnetic separators automatically extract magnetically susceptible tramp metal, such as steel and iron, from the rock stream. Operators select the optimal magnetic separation design based on process and material specifications.
Overband and Suspension Magnets
Operators position overband or suspension magnets above conveyors to attract and remove tramp iron from the conveyed rock. Suspension magnets feature a magnet block that requires manual removal of separated metal, making them suitable for installations with infrequent metal contamination. Overband magnets incorporate a self-cleaning belt that automatically discharges captured metal into a collection area, providing the best option for higher metal contamination levels. Both suspension and overband magnets generate a magnetic field using either an enclosed casing of strategically arranged permanent magnets or an electromagnetic coil wound around a steel core.
Mining and quarrying operations strategically deploy magnetic separation equipment to address diverse operational demands. They favor permanent overband and suspension magnets on mobile crushers and screens, especially in demolition waste recycling and quarry sites. Although some permanent designs function at high suspension heights, operators typically position them within 300mm of the conveyor to effectively remove larger, elongated tramp iron like rebar.
However, many mining operations utilize wide conveyors that transport substantial ore volumes and deep burdens. These conditions necessitate higher suspension heights and create challenging separation environments. Tramp metal frequently settles at the bottom of the burden, requiring a magnetic field strong enough to both attract and move it through the ore. These applications benefit from electro overband or suspension magnets, which generate a significantly deeper and more powerful magnetic field than permanent designs.
When electromagnetic coils project a deep and intense magnetic field, they produce considerable heat. As coil temperature rises, magnetic performance diminishes. Therefore, designers incorporate efficient coil cooling systems using either oil or air. In oil-cooled designs, they immerse the electromagnetic coil in a sealed oil bath within a metal enclosure. The circulating oil transfers heat from the coil to the enclosure’s outer walls, where it dissipates, and the oil cools. For enhanced magnetic performance in smaller coils, they force-cool the oil by passing it through externally mounted radiators and fans.
Designers implement various cooling mechanisms in air-cooled magnets, including fans that blow air directly onto the coil and aluminum fans that radiate outwards. Bunting specifically engineered their air-cooled ElectroMax model as a compact yet powerful electro overband or suspension magnet, ideal for installations with limited space. The electromagnet’s field shape and strength enhance the separation of smaller tramp iron, such as bolts and nuts.
Operators position both permanent and electromagnetic magnets as close as possible to the conveyed material for optimal metal separation. However, material surges can create variable burden depths. When overband or suspension magnets operate at a suspension height near the burden’s top, surges can cause conveyed rock to strike the magnet, damaging the magnet and self-cleaning belt mechanism. Surge protection systems, including sensors that automatically raise the magnetic separator and bars that spread and reduce the burden depth, prevent this damage.
Mining and quarrying installations frequently integrate overband or suspension magnets with metal detectors. The installation’s configuration dictates the metal detector’s placement, either before or after the magnetic separation equipment. In some setups, a metal detector positioned before an electromagnetic magnetic separator identifies tramp metal and signals the magnet to activate. This configuration suits installations with minimal metal contamination and a need for energy conservation. More commonly, the metal detector follows the magnetic separator to detect non-magnetic tramp metal that the magnet missed.
Case Study: Bunting designed and built a 13-tonne Electro Overband Magnet that operates in a gold mine in Northern Finland. Over a twelve-month period, this overband magnet removes damaging tramp metal from approximately 2.7 million tons of conveyed ore, protecting crushers, screens, and other upstream processing plant.
Magnetic Head Pulleys
Operators replace a conveyor’s standard head pulley with a permanent or electromagnetic magnetic head pulley. During operation, tramp iron in the conveyed rock is attracted to and held on the magnetic head pulley’s surface. As the returning conveyor leaves the pulley’s underside, gravity releases the separated tramp iron into a designated collection area.
Larger and heavier tramp metal tends to migrate to the burden’s bottom, making it more challenging to separate using suspension or overband magnets but easier with a magnetic head pulley. Long tramp metal poses difficulties for pulley separation due to limited magnetic field-to-metal contact as it passes over, especially when aligned with the flow.
Magnetic head pulleys suit existing installations with limited space, where installing overband or suspension magnets is impractical. These pulleys feature a continuous magnetic field covering the entire circumference. Permanent magnet designs consist of a solid structure where the entire pulley rotates as one, with the magnet element integrally bound to the outer shell. Electromagnetic versions feature a centralized stationary coil that generates a deep and strong magnetic field, making them suitable for high-volume mining applications.
Because the magnetic separator replaces the head pulley, manufacturers commonly coat the outer shell of both permanent and electromagnetic models with rubber lagging to enhance conveyor grip.
Case Study: Operators utilize two permanent magnetic head pulleys, each 1.2 meters in diameter, at an iron ore mine in Sweden. These pulleys remove large tramp metal from iron ore before crushing and screening. In this application, conveyors measure 1.2 meters wide and travel at 2 meters per second, transporting 650 tons of iron ore per hour with a bulk density of 2.4 tons per cubic meter. Because the pulley magnets function as drive pulleys, manufacturers lag them with rubber to enhance grip on the conveyor belt’s underside.
Drum Magnets
Operators often find drum magnets provide optimal tramp iron separation, although space limitations frequently hinder their installation. Drum magnets feature a centralized, stationary magnetic element (either permanent or electromagnetic) around which a non-magnetic shell rotates. Operators typically feed ore onto the rotating shell’s top via a vibratory feeder. Tramp metal and other magnetic materials attract to the magnetic element and adhere to the rotating shell, discharging when they exit the magnetic field beneath the drum. Non-magnetic material continues its normal trajectory, and a strategically placed splitter separates the two flows.
Drum magnets achieve the highest level of tramp metal separation, as magnetic particles flow close to the magnetic field. Larger diameter drum magnets, rotating at high speeds, process larger volumes of rock. The magnetic field’s close proximity to the rock enables stronger drum magnets, equipped with neodymium magnets, to separate weakly magnetic rocks—the target in numerous mineral beneficiation plants.
Manufacturers offer both permanent and electromagnetic drum magnet designs. Permanent models employ ceramic ferrite and rare earth neodymium magnets to generate either axial or radial magnetic fields.
Axial fields (with poles running across the drum magnet’s width) twist and turn captured tramp metal, releasing any entrapped ore. Radial field drum magnets (with poles running in the direction of flow) achieve the greatest level of magnetic separation but can lead to higher product loss due to entrapment. Typical applications for radial designs include recovering magnetically susceptible ores or removing weakly magnetic minerals from non-magnetic ores.
Metal Detection
Mining operations utilize metal detectors to identify all metal contamination, complementing magnetic separation that removes tramp iron. Metal detectors feature a coil, positioned either under-and-over or beneath a conveyor, through which or over which the conveyed rock passes. Metal detection occurs when tramp metal disturbs the magnetic field generated by the detector coil. Upon detecting metal, the detector sends a signal to a remote control. The control then stops the conveyor and activates an alarm, triggers a diverter gate to reject a material batch, or activates a subsequent overband or suspension magnet.
In large-volume mining operations, operators often cannot halt the conveyor. Instead, they divert a section of metal-contaminated ore into a collection area, where personnel manually inspect the rock or send it through a separate secondary system for tramp metal detection and removal. Designers offer various metal detector designs to suit diverse mining applications.
TN77 Industrial Metal Detectors
The tunnel-type TN77 industrial metal detector provides continuous inspection of non-metallic or non-conductive materials, pinpointing problematic tramp iron and manganese steels. Unlike many other metal detectors, the TN77 indicates the simultaneous detection of one or two tramp metal pieces. The detector also ignores non-magnetic copper-alloy belt fasteners, commonly found in rubber conveyor belts, which can cause false alarms.
Case Study: Plasmor installed three Bunting metal detectors at their building block manufacturing site in Heck, East Yorkshire, UK, to detect tramp metal and protect processing plant equipment. The aggregate mix, which includes clay, Fuller’s earth (an industrial by-product), and recycled dust from the plant’s extraction systems, ensures zero waste production. Plasmor installed the three Bunting metal detectors on three separate material handling conveyors.
Customized Protection: Engineering Solutions for Tramp Metal Control
Tramp metal removal is critical to mining operations. Damage to crushers, screens, and conveyors disrupts or halts production, incurring substantial repair and downtime costs. Furthermore, failure to meet end-customer specifications for tramp metal content, particularly in coal-fired power stations, leads to costly financial penalties or even the rejection of entire material shipments.
Large-scale mining projects frequently necessitate custom-engineered equipment. Bunting’s applications engineering team collaborates closely with contractors and designers to understand project scope. Once they identify challenges, such as deep burden depths or wide conveyors, Bunting’s engineers design optimal magnetic separator and metal detector solutions, often tailored specifically to the project.
Bunting’s team has gained this understanding and knowledge by designing and manufacturing magnetic separators and metal detectors for large mining projects for over 40 years.
Contact our experts to discuss a range of magnetic separation and metal detection equipment designed for the mining industry.
Newton, Kansas – February 10, 2025 – Bunting Magnetics, a global leader in magnetic separation, metal detection, and material handling solutions is launching a new high-intensity Electromagnetic Dry Filter, designed for the separation of fine particles from dry materials across multiple industries.
The advanced filter utilizes electromagnets to generate high background magnetic fields ranging from 3,500 to 5,000 gauss. In combination with the high field gradient on the matrix surface, it effectively separates even the finest iron and paramagnetic particles. It is an ideal solution for recycling, battery production, and mineral processing.
“Our new High-Intensity Dry Electromagnetic Filter represents a significant advancement in magnetic separation technology,” said Adrian Coleman, European Technical Director at Bunting. “By offering a higher separation efficiency than permanent magnetic separators, we’re helping our customers across industries improve product purity and maximize production yields.”
Key Features:
- Background magnetic field strengths of 3,500 to 5,000 gauss.
- Built-in jig for easy maintenance and reduced downtime.
- Automated operation with Siemens S7-1200 PLC and HMI controls.
- Available in capacities from 0.15 to 0.60 m³/hr.
Bunting’s latest innovation builds on the company’s 60-year history of designing and manufacturing magnetic separation equipment. With manufacturing facilities in the United States and United Kingdom, Bunting serves a global customer base across diverse industries.
The Electromagnetic Dry Filter is now available for order worldwide. Discover more about the Electromagnetic Dry Filter by visiting product page.
About Bunting
Bunting Magnetics Co. is a leading manufacturer of magnetic technology solutions for the industrial sector. Headquartered in Newton, Kansas, with multiple manufacturing facilities worldwide, Bunting provides a wide range of products, including magnetic separators, metal detectors, and material handling equipment. The company’s solutions are designed to meet the diverse needs of customers across various industries, from food processing to mining. For more information, visit www.buntingmagnetics.com.
Media Contact:
Jim Thiessen
Corporate Communications
Bunting
800-835-2526
mktg@buntingmagnetics.com
Newton, Kansas – Nov. 18, 2024 – Bunting Magnetics, a global leader in magnetic separation technology, announced the launch of its new high-intensity Electromagnetic Wet Filter, designed for fine particle separation across multiple industries.
The state-of-the-art filter generates a high-intensity magnetic field ranging from 3,500 to 10,000 Gauss, enabling the separation of extremely fine iron and paramagnetic minerals from liquids and slurries. The filter is an ideal solution for ceramics, mineral processing, steel production, water treatment, and recycling.
“Our new Electromagnetic Wet Filter represents a significant leap forward in magnetic separation capabilities,” said Adrian Coleman, European Technical Director at Bunting. “By effectively removing even the weakest magnetic particles, we’re helping our customers across industries dramatically reduce reject rates and rework costs.”
The filter’s advanced design includes highly efficient, computer-designed electromagnetic coils that maintain thermal stability while generating powerful magnetic fields. An oil-cooled system ensures energy-efficient operation at low temperatures.
Key features of the Electromagnetic Wet Filter include:
– Background magnetic field strengths of 2,500, 5,000, or 10,000 Gauss
– Matrix surface magnetic field enhancement of 3-4 times the background field
– Automated operation with Siemens S7-1200 PLC and HMI controls
– Built-in jig for easy maintenance and reduced downtime
– Flexible valve configurations to suit various applications
Bunting’s latest innovation builds on the company’s 60-year history of designing and manufacturing magnetic separation equipment. With manufacturing facilities in the United States and United Kingdom, Bunting serves a global customer base across diverse industries.
The Electromagnetic Wet Filter is now available for order worldwide. For more information, visit the full product page on our website.
About Bunting
Bunting Magnetics Co. is a leading manufacturer of magnetic technology solutions for the industrial sector. Headquartered in Newton, Kansas, with multiple manufacturing facilities worldwide, Bunting provides a wide range of products, including magnetic separators, metal detectors, and material handling equipment. The company’s solutions are designed to meet the diverse needs of customers across various industries, from food processing to mining. For more information, visit www.buntingmagnetics.com.
Media Contact:
Jim Thiessen
Corporate Communications
Bunting
800-835-2526
mktg@buntingmagnetics.com
Newton, Kansas – Oct 28, 2024 – Bunting, a global leader in magnetic separation and metal detection equipment, announces the launch of two upgraded products: the Liquid Magnetic Separator and the Performer Weigh checkweigher. These enhanced models will debut at Pack Expo 2024 in Chicago this November, offering improved performance for food, pharmaceutical, and ceramic industries.
The new Liquid Magnetic Separator, formerly known as the Magnetic Liquid Trap, builds upon its predecessor’s success with advanced features for superior ferrous particle capture. Utilizing high-intensity neodymium magnets, the trap boasts a strength of 10,000 Gauss and 13 pounds of pull, capable of removing even work-hardened stainless-steel particles from liquids, pastes, and slurries. The new Liquid Magnetic Separator will be available globally starting January 2025.
“Our upgraded Liquid Magnetic Separator sets a new standard for magnetic separation in liquid processing,” said Marc Suderman, Product Manager for Magnetic Separation at Bunting. “Its versatility in handling various liquids—from acidic juices to heavy oils—makes it an essential tool for ensuring product purity and safety. Additionally, the new self-cleaning feature is a significant update for the North American market.”
Key features of the Liquid Magnetic Separator include:
- 316 stainless steel construction for durability and compliance with food-grade regulations.
- Available in 2″, 3″, and 4″ line sizes.
- Pressure rating of 10 bars and temperature capability up to 248°F (120°C).
- Optional features such as 150 lb flanges, water jacket, and self-cleaning mechanism.
Bunting’s Performer Weigh checkweigher also receives significant upgrades, integrating advanced metal detection with precise weighing capabilities. The system employs Electro-Magnetic Force Restoration (EMFR) technology, delivering superior accuracy and repeatability compared to traditional strain gauge scales.
“The Performer Weigh represents a leap forward in integrated inspection and weighing technology,” explained Barry Voorhees, Product Manager for Metal Detection at Bunting. “Its combination of metal detection and high-precision weighing in a single unit streamlines quality control processes for manufacturers.”
Notable enhancements to the Performer Weigh include:
- Customizable metal detector aperture for precise contaminant detection
- IP54 rating with IP66 option for increased protection against environmental factors
- High-resolution 15.6″ touchscreen display for intuitive operation
- Multiple reject options and dual reject bins for efficient product handling
- Capacity to process up to 225 pieces per minute
Both products will be on display at Bunting’s booth N-5041 during Pack Expo 2024, taking place from November 3 to November 6 at McCormick Place in Chicago.
About Bunting
Bunting is a leading designer and manufacturer of magnetic separation, metal detection and material handling equipment for the global industrial sector. With over 60 years of experience and manufacturing facilities in the United States and United Kingdom, Bunting provides innovative solutions for diverse industries, including food and plastics processing, recycling, battery manufacturing, and mineral processing.
Product Pages:
Media Contact:
Jim Thiessen
Corporate Communications
Bunting
800-835-2526
mktg@buntingmagnetics.com
Newton, KS – Bunting Magnetics Co., a leader in magnetic technology, is excited to announce the launch of its newly redesigned FF Series Drawer Magnet. The updated design fits more machines, which eliminates the need for customizations. This change not only reduces costs but also speeds up delivery times, providing customers with a more efficient and economical solution. The new standardized FF Drawer reflects Bunting’s commitment to meeting the demands of a broader market.
Since 1966, the FF Drawer Magnet has been a trusted standard in the plastics industry, designed to protect manufacturing lines by removing harmful metal contaminants from product streams. The new design is a direct response to customer and OEM feedback regarding the challenges of long lead times for customized equipment.
A key feature of the new FF Drawer is its universal slotted flange, ensuring seamless compatibility with any square bolt pattern. Additionally, Bunting has standardized its line from six models to just two: High and Low Temperature. The streamlined design makes ordering from Bunting easier, less expensive, and more efficient.
“We are always looking for ways to improve our products to better serve customers,” says Marc Suderman, Product Manager for General Separation at Bunting. “The new design of the FF Drawer Magnet is a result of listening to the direct needs of the plastics industry. It simplifies the entire process, and we believe it will significantly enhance their experience with Bunting.”
The redesigned FF Drawer Magnet is now available for order, marking a new chapter in Bunting’s commitment to quality and customer satisfaction.
About Bunting: Bunting Magnetics is a global leader in metal detection and metal separation technology. They provide magnetic solutions for a wide range of industries, including plastics, recycling, food processing, mining and aggregates, metal stamping, printing cylinders, magnet materials, and more. With a focus on growth and innovation, Bunting has been at the forefront of the magnetics industry for over 60 years.
Product Page: https://buntingmagnetics.com/product/drawer-magnets
Bunting’s Technical Sales Engineer, Peter Buckley, recently conducted a site visit at an animal feed manufacturing facility to inspect the existing Pneumatic Inline Magnets and evaluate a new request. The four (4) PIMs in operation at the plant have been successfully installed over several phases from November 2020 to September 2023.
Inline Magnets are adaptable and economical magnetic separators designed to be integrated into both gravity-fed and pneumatic pipelines. Featuring a plate magnet on one or both sides, they are perfect for extracting occasional ferrous metal contaminants from materials conveyed through pipelines. Made from stainless steel and available in food-grade sanitary options, these pneumatic designs also come with ATEX certification.
Pneumatic Inline Magnetic Separators
The Pneumatic Inline Magnets are installed in pipelines with diameters of 4” (101 mm) and 5” (127 mm). During operation, animal feed is pneumatically conveyed through the center of the housing, passing between two high-strength neodymium plate magnets. Ferrous metal contaminants and other magnetically-susceptible particles, including fine iron, are drawn to the plate magnets’ surfaces and held securely. Regular manual cleaning of the plate magnets, as part of a scheduled maintenance program, ensures the removal of any trapped magnetic particles.
The Pneumatic Inline Magnets are mounted in pipelines measuring 4” (101 mm) and 5” (127 mm) in diameter. As animal feed is pneumatically transported through the center of the housing, it moves between two powerful neodymium plate magnets. These magnets attract and hold ferrous metal contaminants and other magnetically susceptible particles, such as fine iron. To maintain efficiency, a scheduled maintenance program involves the regular manual cleaning of the plate magnets to remove any collected magnetic particles.
“The production and maintenance team are always surprised by the amount of magnetic tramp metal captured by the PIMs,” explained Peter. “Removing the metal not only ensures that the end-product is metal-free, but also prevents damage to other processing equipment. The additional PIM is for a new line as the level of production increases.”
Contact us today to discuss your application or request a quote.
Newton, Kansas – Bunting, a global leader in magnetic solutions, is pleased to announce its acquisition of TD Wright, a premier manufacturer of magnetic printing cylinders. This acquisition, effective immediately, marks a significant expansion of Bunting’s product range, particularly in the printing sector.
Recognized for manufacturing the original adjustable tapered shaft for the metal decorating industry, TD Wright’s flagship ENOC™ System revolutionized the way label changes are performed and has become the industry standard for the Rutherford Decorator. TD Wright also manufactures CD2 and Concord cylinders for the metal decorating industry, as well as CTP cylinders and MMRE rare earth cylinders for folding carton, labeling, and beyond. The TD Wright product line is recognized by the Modular™ Magnetic “checkerboard” design.
“We are thrilled to welcome TD Wright to the Bunting family,” said Robert Bunting Jr., President and CEO of Bunting. “We look forward to building on the legacy David and Joseph McEachern have made in the printing cylinder industry. Their dedication to quality and innovation aligns seamlessly with Bunting’s commitment to excellence. This acquisition enhances our ability to offer customers premium magnetic solutions tailored to their specific needs.”
“With the combined knowledge and precision manufacturing of these two companies, we will be able to support the metal decorating industry and the magnetic cylinder market like never before,” said Joseph McEachern, CEO of TD Wright. “I’m excited for TD Wright to join the Bunting family, and to work alongside Robert and his team as we move forward to produce the best cylinders in the industry.”
Bunting’s acquisition of TD Wright reinforces its position as a leading magnetics company with a global presence. With facilities in North America, Europe, and Asia, Bunting continues to innovate and provide exceptional magnetic solutions for industries worldwide.
For more information about Bunting and its products, Contact Us.
___________________________________________________________________
Contact:
Mark Friesen
Global Director of Marketing
Bunting
Airport Foreign Object Debris (FOD) is a serious issue facing the aerospace and aviation industry. FOD results in an estimated cost of $4 billion annually for maintenance and downtime. FOD is any type of object in an airport setting that has the capacity to cause personal injury or damage to aircraft. Metal contaminants on the runway can result in punctured tires and airframes, the chipping of propeller blades, and even engine failure. During takeoff, the debris on the runaway can be propelled by the jet blast, resulting in the injury of aircraft personnel. Successfully removing harmful metal debris from an airport runway requires creative solutions. Bunting has custom-built and engineered three large and durable Towable Electromagnetic Sweepers (model EMRS24) for removing hazardous ferrous metal debris from an Indonesian airport runway.
Bunting stands as a premier global entity in the realm of magnetic separators, boasting expertise in eddy current separators, metal detectors, and electrostatic separators. Its global manufacturing facilities reside in Newton, Kansas in the United States. The Bunting European manufacturing facilities are in Redditch, just outside Birmingham, and Berkhamsted, both in the United Kingdom.
The Towable Electromagnetic Sweeper is engineered with a specific aim: to remove ferrous debris from a variety of surfaces including airport runways, roads, shipping ports, expansive car parks, and sizable warehouses or manufacturing facilities. Its functionality hinges on an intricately crafted electromagnetic block, meticulously designed to generate a robust magnetic field capable of efficiently lifting and retaining both large and small ferrous metals.
Bunting Towable Electromagnetic Sweepers were Custom-Built for an Indonesian Airport
During operation, the Towable Electromagnetic Sweeper seamlessly affixes to the rear of a vehicle, whether it’s a service vehicle or SUV. Supported by two sturdy wheels and featuring a user-friendly tow hitch, the primary magnetic block ensures a quick and secure connection. As the sweeper functions, it efficiently lifts ferrous metal debris from the ground onto its magnetic surface. Positioned within the vehicle cab for easy access, controls empower the operator to activate or deactivate the magnet, enabling the swift release of any trapped ferrous metal debris.
Towable Electromagnetic Sweepers are designed for outdoor use, ideal for towing at speeds ranging from 5 to 6 mph. Available in a variety of widths, ranging from 1200mm to 2440mm, these sweepers can also be tailored to meet specific requirements through custom designs.
The trio of Electromagnetic Sweepers commissioned for Indonesia boasts a magnetic width of 2440mm each, weighing approximately 1500 kg. Powering the electromagnet is a 220VAC generator, coupled with a gasoline-driven Honda engine nestled within a protective framework. The start and stop push button feature auto-reverse functionality, facilitating the lifting and release of captured tramp ferrous metal. A rotating flash beacon atop the control panel serves as a visual indicator of the magnet’s operational status.
“We design and build Towable Electromagnetic Sweepers for airports around the world,” says Phil Tree, Bunting’s Technical Sales Manager. “This is a practical method of clearing runways of ferrous metal detritus and preventing dame to aircraft tires.”
Contact us today to discuss your application or request a quote.