Separating Fine Iron from Powders with Metal Detection and Magnetic Separators
It is challenging to effectively separate fine iron from dry powders. Sometimes, even the strongest magnetic separators may struggle or even fail to successfully remove the smallest of magnetic particles. To find a successful solution, it is important to first fully understand the way fine materials behave. Only then does it become possible to determine the optimum method to cleanse powder of problematic fine iron.
What is a Powder?
Dry powders are used in many industries, including food, pharmaceuticals, chemicals, and refractories.
In industry, “powder” is defined as fine, dry particles that are produced by crushing, grinding, or disintegration of a solid substance. The processing and handling of powders can often be challenging, as bulk powders exhibit similar properties to both liquids and solids.
Metal Contamination
Metal contamination, most commonly in the form of iron, can occur at any stage within a powder processing operation. If larger tramp metal, such as rust, nuts, nails, and other larger pieces of scrap, can remain undetected, it then enters the size reduction stage. This tramp metal often goes on to damage process equipment if it is not stopped. Here, magnetic separators and metal detectors are installed to capture and remove metal particles. If it passes through this stage, tramp metal often becomes significantly reduced in size and increasingly difficult to extract as a result.
Magnetically susceptible metal contamination (i.e. iron) is commonly removed using magnetic separators. There are some magnetic separators that produce a magnetic field using an electrical current, but the vast majority utilize permanent magnets such as ceramic ferrite and rare earth neodymium iron boron. Ceramic ferrite magnets produce magnetic fields that are deep, but low strength. Neodymium magnets are the strongest magnets commercially available, and are able to produce the strongest permanent magnetic fields as a result.
Where Does Metal Contamination Come From?
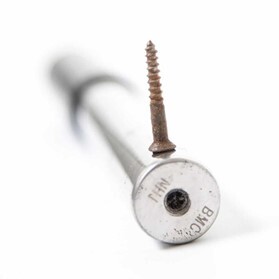
Metal contamination in bulk powder commonly comes from:
1. Primary large tramp metal such as nails, screws, and bolts.
2. Primary fine iron or magnetic particles present in the raw material. This metal originates from primary processing, transportation, and can even occur naturally in the original material.
3. Secondary fine iron originates from larger tramp metal (such as primary large tramp iron) that has been reduced in size as a result of the powder manufacturing process. This could typically originate from a nail, screw, or bolt that has been processed through a crusher. It may also originate from damaged or worn processing equipment. Another common source of secondary fine iron contamination is rust. Rust can fall into the material processing line from worn and weathered processing equipment such as chains, hoists, and building cladding.
It is easier to separate and detect tramp metal when metal contamination is present in a larger form, where it can then be successfully removed using a wide range of magnetic separators and metal detectors. Magnetic separation that utilizes standard strength ceramic magnets with deep magnetic fields are ideal. A good example of this sort of magnetic separator is the plate magnet, often installed in a chute, in a housing, or as part of an in-line magnetic separator.
Metal Detectors
It is easier for a metal detector to detect larger metal contamination. As metal passes through the coil of the metal detector, it is sensed and then removed from the flow by means of an automatic reject system. For detection, the magnetic field generated by the metal detector must see a state change. Since finer sized metal produces a lesser state change, it is more difficult to detect.
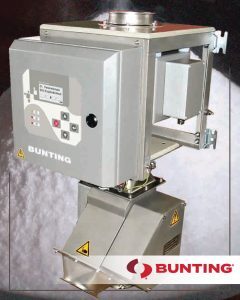
The accompanying photo in the text shows a processor of Sodium Bicarbonate using a QuickTRON 05 metal detector to remove larger pieces of tramp metal.
By removing larger tramp metal with magnetic separators and metal detectors prior to the processing stage, metal is not only prevented from being reduced in size (e.g. converted into a secondary source of fine iron contamination), but it also protects delicate processing equipment such as shredders, crushers, and mills from being damaged by the metal.
Once material is in a powder form, there are important processing parameters to consider when the optimum method to remove fine iron contamination is being assessed.
How Does a Powder Flow?
Powder remains light and free when it is sprinkled. However, when the same powder is compressed or vibrated, it can become very dense and even lose its ability to flow.
Individual grains in bulk powders cling to each other in clumps. This is in accordance with the Van der Waals force. This kind of coagulation often results in fine iron becoming trapped among clean product. The ability of any magnetic separator to successfully hold, attract, and separate fine iron is dependent on iron being as close to the magnetic field as is physically possible. Fine iron that comes into contact with the surface of a magnetic separator with a high strength magnetic field will be securely held in place. However, if fine iron is trapped inside a coagulation of powder, it may be held out of reach of the maximum magnetic force. As a result it will not be separated.
The design of the magnetic separator is impacted by the way that bulk powders flow. The design of a magnetic separator may exacerbate classic problems that powders flowing in a hopper may experience, such as bridging, rat holing, or flooding.
Different Designs of Magnetic Separators
High strength magnetic fields, as produced by rare earth neodymium magnets, are necessary to capture fine iron metal contamination.
1. Tube Magnets (also known as rod magnets and cartridge magnets), typically placed in a multi-rod grate configuration.
2. Tapered-faced plate magnets.
3. Center flow magnets housed inside a tubular body.
4. Drum magnets with a fixed, curved magnetic arc positioned within an independently rotating outer shell.
Tube, Grate, and Drawer Filter Magnets
While a tube magnet may occasionally be used on its own, it is more commonly part of a larger, multi-cartridge grate system. Magnetic grates are designed to fit inside a hopper, but can also be supplied complete with a housing (such as in the case of a Drawer Filter Magnet).
When in operation, powder freely falls onto the surface of the tube magnet where fine iron strikes the surface. It is then held by the strong magnetic field. Deflectors are often deployed above the gaps, between the tubes, in order to ensure that the powder makes contact with the tube surface.
Drawer Filter Magnets
The separation efficiency of a tube magnet will be reduced if powder is allowed to build up on its surface. In severe cases, a slight build up on the surface of a tube can quickly result in a blockage of the whole housing.
Tapered Step Plate Magnets
When it is possible for material to flow over a surface, it is ideal to implement flat-faced plate magnets. To capture finer iron, rare earth neodymium plate magnets can be used. Their powerful magnetic field becomes further enhanced when a tapered step is added to the magnet’s face. Captured iron migrates behind the step and away from material flow, which reduces the risk of it re-entering the cleansed product.
In-Line Magnetic Separators
Plate magnets are not only fitted into chutes, but are also incorporated into housings as In-Line Magnets. In-line magnets are able to remove tramp iron and ferrous fines from flow-resistant bulk powders without restricting flow. There are two designs of in-line magnet:
1. Gravity In-Line Magnets (GIM)—In gravity in-line magnets, plate magnets are positioned in round, sloping spouting where material is under gravity flow. Spouting should be angled no more than 60° from horizontal in order to enable effective tramp metal capture.
2. Pneumatic In-Line Magnets (PIM)—Pneumatic in-line magnets are designed to be used in dilute phase pneumatic conveying systems, up to 15psi. They work best in horizontal runs with the plate magnet down to take advantage of material stratification. They can easily be installed with optional factory-supplied compression couplings.
Center Flow Magnets
The center flow magnet features a centrally located cone-shaped magnet within a tubular housing. Center flow magnets are used widely in the bulk handling industry. The way the magnetic cone is positioned allows for powder to flow free of obstruction.
This conical magnet is suspended in the center-line of the housing, which ensures maximum contact with the flow of the product. The magnet is tapered, with an exposed-pole and a stainless steel “nose cone” that allows it to direct the flow of materials around the magnet. The cone magnet’s tapered poles allow ferrous fines to be collected out of the direct air stream. In addition, the trailing end of the magnet is an active magnetic pole. This magnetic pole holds any tramp metal that is swept down the cone.
Drum Magnetic Separators
High strength, permanent drum magnets can enable the optimum level of separation when used in specific applications. The drum magnet is gravity-fed, usually by a vibratory feeder. Drum magnets have a stationary, high-strength magnetic arc that is positioned inside a rotating outer shell. The stationary magnetic assembly inside the shell projects a strong magnetic field, and when material flows onto the surface of the drum magnet, it attracts and securely holds fine iron to the stainless steel surface of the drum. Once contaminants have been captured, clean product is allowed to freely fall to a discharge point. While the drum is rotating, the fine iron it has captured travels along the drum surface and out of the magnetic field, where it is then discharged.
Various magnetic field configurations for a drum magnet are possible. The configuration that produces a radial magnetic field is the one most suitable for removing iron from bulk powders. This ensures that once fine iron particles have been captured, these contaminant particles do not leave the drum surface until they move out of the magnetic field.
Several challenges must be overcome when processing bulk powders on a drum magnet.
Feeding the Drum Magnet
If the operator does have a way to steadily feed the drum with low amounts of product, Bunting recommends that the vibratory feeder is equipped with an air bed in order to produce a consistent feed of powder. Standard vibratory feeders may deliver powder in clumps, which can significantly affect separation performance.
Drum Shell Rotating Speed
A drum magnet’s shell should be rotated at consistently high speeds. This results in some powder pluming, although this can be minimized by keeping the distance between the rotating surface of the drum magnet and the end of the vibratory feeder tray to a minimum.
The drum magnet’s high rotation speed significantly reduces the amount of product that is lost to the magnetics. Since there is less material on the drum’s surface at any given time, the chance of entrapment is reduced.
Drum magnets operating at high rotational speeds have been highly successful in removing fine iron from refractories, abrasives, and other applications where the material has a high specific gravity.
Magnetic Separators and Metal Detectors for Powder Purification: Ensuring Bulk Powders are Metal-Free
As the demand for finer and purer powders increases, the need to remove the finest iron increases as well. It is vitally important to understand the powder’s properties and behavior when considering the optimum method of fine iron separation. Often, the ultimate solution is to install a series of magnetic separators and metal detectors at key strategic points within the process.
To learn about Bunting’s ability to custom design magnetic separators and metal detectors to remove contamination in your powder plant, Contact us Today.