Permanent Drum Magnets
Magnet | Ferrite, Neodymium |
Materials | Dry |
Conveying | Gravity, Belt, Screw, Vibratory Feed |
Separates | Ferrous tramp |
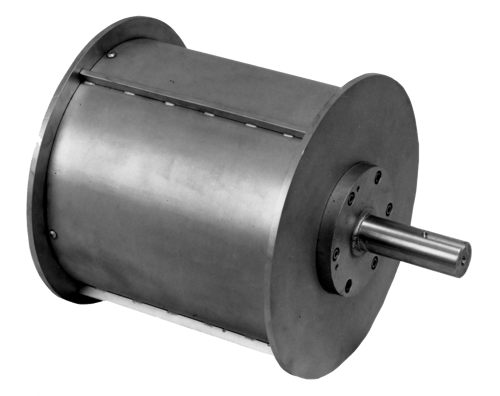
Options / Features
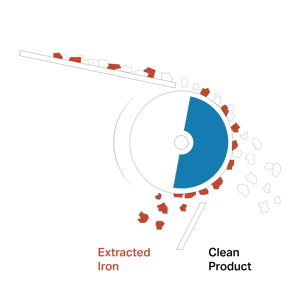
For removing smaller, weakly magnetic particles
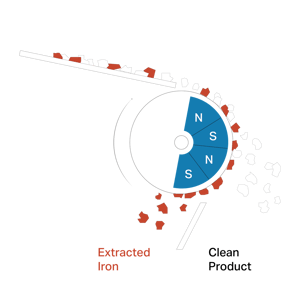
Flips the ferrous metal to reduce product entrapment.
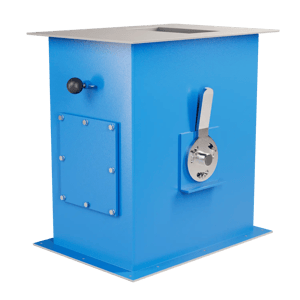
Drums can be supplied with or without housing
Animation
- About
- Benefits
- Tech Specs
Industries: food processing, plastics, recycling, grain and milling, powder and bulk solids, aggregates, mining, minerals, ceramics
The Drum Magnet by Bunting is a high-efficiency magnetic separator designed to remove ferrous metal contaminants from a variety of product streams. This separator ensures product purity and protects processing equipment from potential damage.
These magnets continuously capture and discharge ferrous contaminants without interrupting product flow. As material passes over the drum, magnetic particles are attracted and held to the drum's surface (radial pole design), while non-magnetic material flows freely to the discharge point. Cleats on the drum assist in sweeping the captured metal out of the magnetic field, ensuring continuous self-cleaning operation.
By integrating the Drum Magnet into your processing line, you enhance product quality, ensure compliance with industry standards, and extend the lifespan of your equipment.
Continuous, Automated Operation
Eliminates the need for manual separation or downtime—ideal for high-volume, 24/7 operations.
Reduced Equipment Wear and Maintenance
By removing ferrous metals upstream, drum magnets protect shredders, grinders, screens, and other downstream equipment from damage and costly repairs.
Increased Product Purity
Ensures cleaner output by effectively separating even weakly magnetic or fine ferrous contaminants.
Energy-Free Magnetic Power
Fully permanent magnet systems require no electricity to operate, lowering operating costs and simplifying integration.
Flexible for Any Application
Available in a range of diameters, widths, magnetic strengths, and field configurations (axial or radial) to match your specific material and flow characteristics.
Low Maintenance and Long Lifespan
With no moving internal parts and wear-resistant components, Bunting Drum Magnets offer years of reliable, maintenance-light service.
Designed for Harsh Environments
Built tough to handle abrasive, dusty, or moisture-prone materials commonly found in recycling, mining, and plastics processing environments.
Precision Separation with Adjustable Splitter
Customize the split point between magnetic and non-magnetic fractions for more efficient recovery and minimal product loss.
Advantages Over Electromagnetic Options
- No Power Required: Fully permanent magnetic design
- Low Maintenance: No cooling systems, coils, or control panels to manage
- Long Service Life: Field strength does not degrade over time
Magnet Type
Ferrite
High Intensity: Rare Earth (Neodymium)
Magnetic Field Configuration
Axial: Polarity runs along drum width
Radial: Poles run vertically down the drum
Drum Diameter
Up to 1500mm (60")
Drum Width
Up to 2400mm (96")
Shell Material
Non-magnetic stainless steel
Magnetic Arc
120-degree to 190-degree
Application Photos

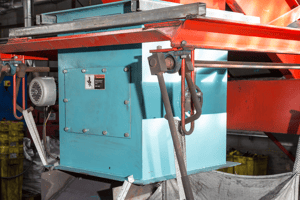
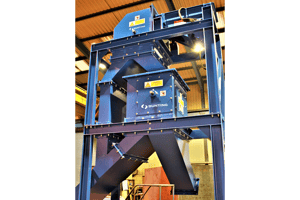
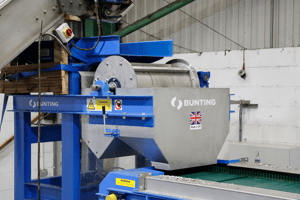
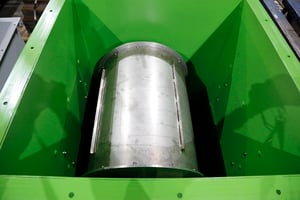
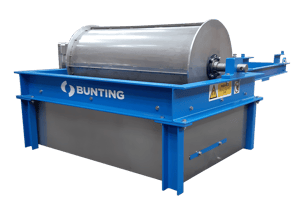
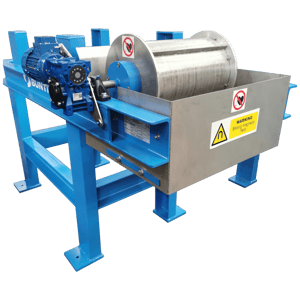

Talk to an Application Engineer
Not sure what you need? Let’s talk through your application and identify the right solution.