Practically Measuring Magnetic Separator Strength
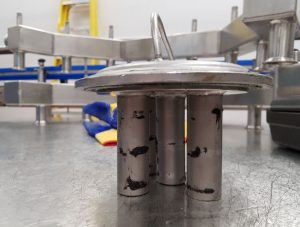
A Magnetic Separator is designed to attract, capture and hold magnetic particles. The magnetic strength needed to successfully achieve that design objective is commonly stated in a magnetic separator supplier’s quotation or specified in the tender. This ‘Magnetic Strength’ is usually referenced in terms of ‘gauss,’ a unit of measurement. However, the ‘gauss’ value can be very difficult to accurately measure.
There is a more practical method of assessing the magnetic strength. This removes any ambiguity while providing simple, repeatable, and comparable data to assess most Magnetic Separators.
Accurately testing the strength of your Magnetic Separator is crucial to the success of your operation
Measuring Magnetic Strength
The magnetic strength of a Magnetic Separator is often referenced in terms of ‘gauss’. Gauss (symbolized G) is the centimeter-gram-second (cgs) unit of magnetic flux density. A flux density of 1 G represents one maxwell per centimeter squared (1 Mx cm -2 ). It is named after the German scientist Carl Friedrich Gauss.
Gauss can be measured using a Gaussmeter. However, it is important to note that the Gauss rating on its own does not fully indicate the strength of a magnet. Additionally, gaussmeters can give a range of readings dependent upon the orientation of the probe and several other variable parameters.
Proposals for Tube Magnets often include details of length, diameter and the gauss reading. With the gauss reading being so difficult to test and prove, purchasers and users are unable to check that the Tube Magnets supplied actually meet the specification of the quote and the order.
However, in terms of Magnetic Separation the objective for the user is simple; the magnetic force must enable the attraction and capture of any magnetically susceptible metal. That ability can be measured as a function of the effort needed to remove a specific steel item from the surface.
The Method
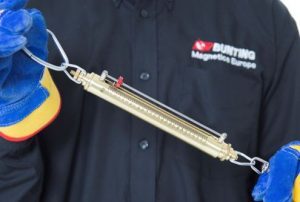
Measuring the effort needed to remove a steel item from the face or surface of a Magnetic Separator is achieved using a spring balance and is commonly called a ‘Pull Test.’ The magnetic test piece (e.g. a 6mm ball bearing welded onto a non-magnetic attachment ring) is clipped onto the end of the spring balance.
The magnetic test piece is placed on the surface of the Magnetic Separator and force applied at the other end of the spring balance until it is detached. The force required to remove the magnetic test piece (measured in kgs) is recorded on the measurement scale of the spring balance.
Measurements are taken in the center of the Tube Magnet and on the end poles. They are repeated three times and the average recorded as the force required to remove the magnetic test piece at each point.
The following video explains the Pull Test technique.
This simple but effective method does not record or provide any indication of the gauss, but accurately provides data that can be used to compare the condition of a Magnetic Separator over time and compare the performance with other similar designs.
Pull Test Experiments
Magnetic Separator designs vary considerably depending on the application. The Pull Test technique is suitable for measuring the magnetic strength of smaller Magnetic Separators such as Tube or Cartridge Magnets and Plate Magnets.
Tube or Cartridge Magnets are often used stand alone or as part of a Magnetic Separator configuration (e.g. Drawer Filter or Liquid Trap).
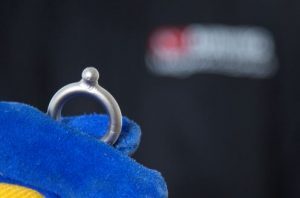
A small steel ball is used as the magnetic test piece when measuring the magnetic strength of a Tube or Cartridge Magnet (the photograph shows a 6mm diameter ball)
The metal test piece is attached to the end of the Spring Balance and then placed into the magnetic field, being attracted to the magnetic pole.
In a series of experiments, we used the Pull Test technique to assess the magnetic strength of Tube Magnets with Ceramic (Ferrite), Standard Neodymium Rare Earth, and High Strength Neodymium Rare Earth Magnets.
The tests were undertaken using three different sizes of steel ball in the magnetic test piece (6mm, 12mm and 25mm) and introduced non-magnetic spacer to assess the magnetic strength at specific distances away from the surface (3mm and 6mm). All the recorded measurements are in kilograms (kg)
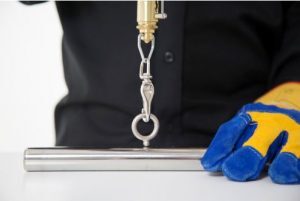
Ceramic (Ferrite)
Gap | 6mm Ball | 12mm Ball | 25mm Ball |
None | 1.25 | 1.75 | 2.5 |
3mm | NR | NR | 1.2 |
6mm | NR | NR | NR |
Standard Neodymium Rare Earth
Gap | 6mm Ball | 12mm Ball | 25mm Ball |
None | 2 | 4.25 | 9 |
3mm | 1.2 | 1.6 | 2.45 |
6mm | NR | 1.25 | 1.5 |
High Strength Neodymium Rare Earth
Gap | 6mm Ball | 12mm Ball | 25mm Ball |
None | 3.75 | 9 | 14.5 |
3mm | 1.5 | 2.5 | 4.6 |
6mm | 1.1 | 1.5 | 2.25 |
In all cases, the drop off in magnetic strength as you move away from the surface of the Tube Magnet is significant and this highlights the need for metal contamination to come into contact with the surface. Arrangements where the Tube Magnets are configured as a Grate (i.e. are lined up and equally spaced) commonly have a deflector above the gap between the Tubes that directs material in the area of maximum magnetic strength.
The tests highlight the difference in magnetic strength on the surface, with high strength Rare Earth magnets producing nearly 3 times as much pull as Ceramic magnets.
Findings During Magnetic Separator Audits
Magnetic Separator Audits often highlight issues that had previously gone undetected. The first check focuses on the physical integrity of the Magnetic Separator, inspecting welds, and assessing wear and damage. Once these have been completed, the measurements are taken.
The most common findings when undertaking magnetic separator audits are:
Weld Failure
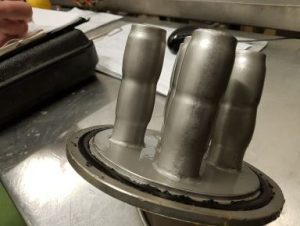
Magnetic Liquid Filters, fitted into pipelines, have Tube Magnets that are welded to a lid and project down into the product flow. Metal is attracted and captured on the surface of the Tube Magnet.
In cases where the welds have failed (e.g. poor manufacture, eaten away by acidic or alkaline liquids), liquid will seep into the tube and onto the magnets. The magnets then swell and lose magnetic strength, ultimately splitting the outer stainless-steel casing.
Tube Magnet Wear
When material falls directly onto the surface of a Tube Magnet, over time the surface can be worn. Wear usually occurs on the poles where magnetic particles have been captured. Once the outer stainless-steel casing has been breached, the Tube Magnet should be replaced.
Weak Tube Magnets
Magnetic separation audits highlight the variance in magnetic strength of Tube Magnets. Often, the Tube Magnets have been installed for some time and details of the original specification have been lost. When testing the magnetic strength, some Tube Magnets are found to have very poor strength and provide little if no metal separation protection. This is of great concern when the Tube Magnet is positioned to protect a particular item of processing plant where metal contamination damage could result in production downtime and costly repairs.
Conclusion
The Pull Test Experiments highlight the importance of physically checking the real magnetic strength of a Tube Magnet and not only relying on the stated gauss. Including details of the force needed to detach a 6mm steel ball from the surface of the Tube Magnet in the request for quotation and the order, protects the user and ensures that the supplied equipment is as exactly as stated.
This ‘Pull Test’ measurement technique also enables a regular comparative test that will immediately highlight any drop in magnetic strength. This can be used in annual audits or inspections as part of a plant’s quality management system. A change in ‘pull’ strength may be the result of physical (e.g. failed weld, broken magnets from being dropped) or excessive heat. The reduced magnetic force may result in the magnetic separator no longer being fit for purpose.