Metal Recovery from Electric Vehicles – Magnetic Separation
This article was originally written by Professor Neil Rowson, Emeritus Professor in the School of Chemical Engineering at the University of Birmingham, and has been rewritten to suit a US audience.
Mining the Urban Environment
Raw material reserves have been put under a huge strain due to the anticipated global increase of production and consumption of electric vehicles and other electronic goods. As a result, manufacturers are turning away from simply determining better ways to mine raw minerals, and are instead seeking out ways to better reclaim, reuse, and recycle secondary materials. This has become known as “Mining the Urban Environment.”
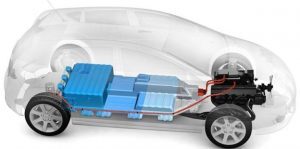
Many governments have sought to partially control some secondary material supply chains. This is because critical metals have high strategic value.
A great deal of high-tech products, high-value waste streams, and electronics industries have already established recycling routes. For example:
• Recycling of platinum group metals from auto-catalyst
• Recovery of platinum group metals from road dust
• Recycling of specific items from gasoline and diesel-powered cars, such as batteries (Lead)
• Auto-catalyst (Pt, Pd, Rh), radiator (Cu), and general base metal recycling
• Processing of electronic waste (WEEE) (Cu, Al, Ag, Au, Platinum Group Metals)
• Domestic battery recycling (Lithium and other metals)
• Plastic and glass recycling (mature technology)
As new technological developments occur, the recycling landscape is constantly changing in response. New technological developments can alter both the location and amount of valuable metals that can be present in a waste product. Frequently, this leads to increased complexity of metal recovery. Ongoing changes present enormous ongoing challenges to the recycling industry. Some examples of metals expected to be of high value in the future include:
• Platinum group metals from medical waste
• Rare earth elements originating from auto waste, computer hard drives, mobile phones, wind turbines, etc.
• Graphite from steel waste (Kish graphite)
• Lithium, cobalt, graphite, and nickel from Li-ion car batteries
• Germanium/gallium from coal fly ash
Successful “urban mining” is able to reduce demand on primary raw material reserves by successfully recovering metals and other valuable materials from waste. Urban mining is also able to broaden the source location of materials, and typically trends towards source locations becoming more localized. This leads to transportation costs being reduced and prices stabilizing. This is particularly beneficial in the case of geographically limited materials such as neodymium magnets, of which over 90% are currently supplied from China.
For |
Against |
Less Processing, especially Primary Raw Materials |
De-Stabilize Metal Markets |
Reduced Carbon Footprint |
Reduce Platinum Group Metal Demand for Primary Producers |
Higher Material Grades | Processing Locations often in Areas of High Population |
Lower Cost per Ton of Material |
|
Reduced Transportation |
|
Sustainable Production meeting Increased Demand for Metals |
|
Allows each Country to set a Strategic Plan for Key Materials |
Definition of Critical and Strategic Materials
When considering urban mining, the European Union has produced critical assessments based on economic importance and supply concerns for key materials. These assessments are updated on a regular basis.
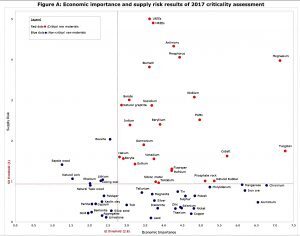
When carrying out assessments, the European Union identified rare earth elements as a highly critical material. The United States Department of Energy and Department of Defense have also identified rare earth elements as a critical material. Rare earth elements are key components in the manufacturing of items such as electronic goods, computer hard drives, wind turbines, and electric/hybrid vehicles.
A much greater quantity of rare earth magnets is used in electric and hybrid vehicles as opposed to traditional combustion engines. In order to address anticipated supply issues of rare earth elements, the EU is currently funding research projects such as SUMSAGPRO and DEMETER. Bunting is a key member and contributor to DEMETER as well as the Magnet Materials Group (MMG) at the University of Birmingham. The primary goal of these groups is identifying processes to recover, reuse, and/or recycle rare earth magnets from secondary sources, in addition to developing technology that will create a new generation of “recycled” magnets that are able to achieve the same magnetic performance as magnets made from primary materials.
Rare Earth Magnets in Electric Vehicles
Rare earth magnets (neodymium and samarium cobalt magnets) are critical to many key components of electric vehicles. They can be found in motors including power-steering motors, stop motors, windshield wiper motors, electric windows, and drive motors. They can also be found in generators, such as regenerative braking systems and range extenders. Rare earth magnets are also essential to speakers and many other small motors found in electric vehicles. Each new electric car that is produced is estimated to contain between from 4 to 11 pounds of rare earth magnets.
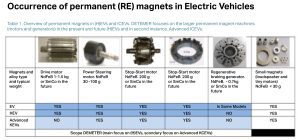
Critical Materials
The EU lists platinum group metals (PGMs—platinum, palladium, rhodium) as critical and strategic materials. These metals are key components in capacitors and sophisticated electronic components. PGMs are increasingly becoming more common in auto-shredder residues as well as electronic waste streams. Due to the high market price of PGMs, recycling companies are becoming increasingly interested in these materials.
Lithium-ion batteries, known for their recharging capabilities, are also being used more and more. Lithium batteries can be found in electronic goods such as mobile phones, power tools, cameras, laptop computers, and many other everyday items. As electronic vehicles grow in popularity, the demand for rare earth magnets used in electric vehicle drive motors as well as the demand for lithium batteries is expected to sharply increase. If demand increases as it is expected to, there could be potential future supply issues for ethically sourced materials such as graphite, nickel, cobalt, and lithium.
Additionally, as electric and hybrid vehicles will inevitably begin to arrive at auto recycling facilities, even more new challenges will present themselves. Because the nature of the materials has changed, and secondary materials have simultaneously seen an increase in value, the recycling of high value components will become more economically viable as a result.
Challenges facing car recyclers with the onset of electric vehicle recycling
Reuse versus Recycle
Eventually, the operating efficiency of Li-ion automotive batteries will drop below a specified level, at which point replacement becomes the only option. What happens to the removed batteries next is dependent on the condition of the batteries as well as any dead cells. Currently, the most favorable option is for the battery to be reused in a less demanding application. Many companies are now offering this service, which repurposes functioning batteries for less demanding power storage on a global scale. However, once a battery’s useful life completely comes to an end, the battery must be safely disposed of or recycled—preferably, recycled.
The main commercial and ethical drivers for the reuse and recycling of batteries include:
• Lower CO2 cost.
• Access to and control of critical materials and strategic elements.
• Ethical concerns of mining raw materials, including welfare of workers and local communities as well as environmental costs.
• Potential difficulties exporting battery waste. For example, BREXIT may cause difficulties with exports to the EU, and countries such as China are continuing to impose stricter restrictions regarding accepting imported waste materials.
• Sustainable use of Earth’s resources (including cobalt, graphite, and lithium).
Structure and Chemistry of Lithium-Ion Vehicle Batteries
The chemistry and design of electrical vehicle batteries is evolving continuously, and seeing ongoing improvements in operating efficiencies.

Conventional Li-ion battery designs consist of:
• Graphite coated copper foils to form anodes.
• Aluminum foil coated in oxides of manganese, cobalt, and nickel to form the cathode.
• The electrolyte comprises Lithium hexafluorophosphate (LiPF6) dissolved in a mixture of organic carbonates. The mixture mostly contains ethylene carbonate, diethyl carbonate, and ethyl-methyl carbonate with trace additives for electrolyte performance.
A Li-ion car battery’s battery pouch will vary in chemistry and design depending on the individual vehicle manufacturer’s specifications.
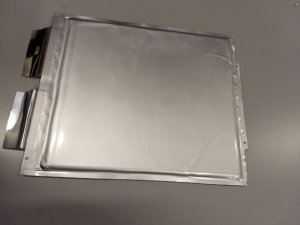
The first step in the recycling process is to safely discharge the battery pouch. After being discarded, the pouch is shredded and dried, leaving behind a mixture of anode material, cathode material, plastics, and black powder (black mass). This process is very similar to the process of recycling WEEE, or electronics waste.
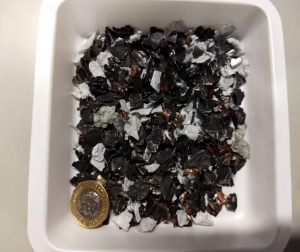
After individual materials have been liberated by shredding, physical separation techniques are applied to enable segregation of material into concentrations of anode, cathode, plastic, and black mass. The shredded battery’s particle distribution is determined by the shredded blade geometry and screening. Physical separation technology utilized in this process includes magnetic separators, eddy current separators, and electrostatic separators.
In order to effectively recycle li-ion vehicle batteries, the waste must be physically processed correctly. By using the correct combination of shredding, physical segregation, and sorting by means of magnetic separation and eddy current separation as two key equipment types, metallic and metal oxide materials will be effectively separated and concentrated from the battery structure.
Why the Physical Separation Route to Recycling?
There are many important benefits to be gained by recycling batteries using physical separation techniques:
• There is no change to the material’s structure or chemistry.
• Separation can take place based on different physical properties of the material.
• Low energy use.
• Low operating costs.
• Adapts existing technology with proven results.
• Reduces overall processing costs by enabling the concentration of individual materials for expensive downstream processes.
Typical Separation Equipment for Electric Vehicles
Ferrous and Non-Ferrous Metal Separation
In 2018, the ReLib Li-ion car battery recycling research project partnered with Bunting to create a pilot plant scale metal separation module. This example of a metal separation module in a battery recycling application incorporates a high strength rare earth drum magnet and an Eddy Current Separator. This module is able to separate plastic pouch material and polymer battery structures from the anode and cathode materials.
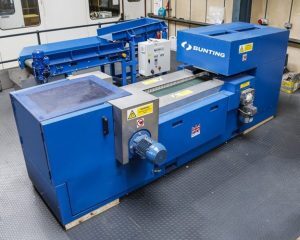
During operation, a vibratory feeder evenly feeds shredded material onto a drum magnet’s rotating surface. Strongly magnetic and weakly magnet materials are then attracted, held, and then deposited away from the remaining non-magnetic material.
Click for Technical information on the Eddy Current Separator
During the second stage, the Eddy Current Separator separates non-ferrous metals.
An Eddy Current Separator is designed to have a short belt conveyor, positioning a drive at the return end and installing a high-speed magnetic rotor system at the discharge end. Within a separately rotating non-metallic drum, there is a magnetic rotor. This rotor revolves at approximately 3000 revolutions per minute while operating, while the outer drum cover rotates at the same speed as the belt conveyor.
As the rotor of the Eddy Current Separator spins, an electric current is induced into any conducting metals, such as zinc, copper, and aluminum. This induced electric current produces a magnetic field, which then opposes the field created by the rotor and results in the conducting metals being repelled over a pre-positioned splitter plate. Then, the remaining materials will fall in a normal trajectory away from the separation area, effectively separating them from the repelled metals.
Summary
The popularity of electric vehicles increases more and more with each passing year. As more electric vehicles are purchased and used by consumers, the number of electric vehicles reaching the end of their life and requiring that they be effectively recycled will increase as well. Reusing batteries from electric vehicles is by far the preferred option, but eventually, nonviable batteries must be safely disposed of and recycled. While this is a very new industry, Bunting magnetic separation environment has already proven to be a valuable tool in electric vehicle recycling and urban mining.
This article was originally written by Professor Neil Rowson, Emeritus Professor in the School of Chemical Engineering at the University of Birmingham, and has been rewritten to suit a US audience.